Spinning oil and preparation method thereof
A technology of spinning oil and lauryl oleate, which is applied in the field of textile additive preparation, can solve the problems of not being able to improve spinning performance and limited effect, and achieve an increase in elastic recovery rate, a reduction in boiling water shrinkage, Good performance
- Summary
- Abstract
- Description
- Claims
- Application Information
AI Technical Summary
Problems solved by technology
Method used
Image
Examples
Embodiment 1
[0017] A kind of spinning finish, comprising by weight components: 50 parts of lauryltrimethylammonium chloride, 10 parts of lauryl oleate, 10 parts of polyoxyethylene oleate, 1 part of lauric acid diethanolamide, 1 part of sodium dodecylbenzenesulfonate, 0.5 parts of octyl phosphate, 15 parts of lauryl oleate, 6002 parts of polyethylene glycol, 16 parts of dimethyl siloxane, 2 parts of sodium polymethacrylate, Dioctyl phthalate 3 parts.
[0018] The preparation method of above-mentioned spinning oil agent, step is as follows:
[0019] (1) take each component according to parts by weight;
[0020] (2) Add lauryl oleate, polyoxyethylene oleate, octyl phosphate, lauryl oleate, polyethylene glycol 600 and dioctyl phthalate into the reaction kettle, heat to 70 ℃, stirring for 20 minutes;
[0021] (3) Add the remaining components to the mixture obtained in step (2), stir at 70° C. for 10 minutes under a vacuum of 0.03 MPa, then cool down to 40° C., and stir for 30 minutes under ...
Embodiment 2
[0023] A kind of spinning finish, comprising by weight components: 52 parts of lauryltrimethylammonium chloride, 15 parts of lauryl oleate, 13 parts of polyoxyethylene oleate, 2 parts of lauric acid diethanolamide, 2 parts of sodium dodecylbenzenesulfonate, 0.8 parts of octyl phosphate, 18 parts of lauryl oleate, 6005 parts of polyethylene glycol, 23 parts of dimethyl siloxane, 3 parts of sodium polymethacrylate, Dioctyl phthalate 5 parts.
[0024] The preparation method of above-mentioned spinning oil agent, step is as follows:
[0025] (1) take each component according to parts by weight;
[0026] (2) Lauryl oleate, polyoxyethylene oleate, octyl phosphate, lauryl oleate, polyethylene glycol 600 and dioctyl phthalate are added to the reaction kettle and heated to 72 ℃, stirring for 23 minutes;
[0027] (3) Add the remaining components to the mixture obtained in step (2), stir at 72° C. for 15 minutes under a vacuum of 0.03 MPa, then cool down to 43° C., and stir for 32 min...
Embodiment 3
[0029] A kind of spinning finish, comprising by weight components: 56 parts of lauryltrimethylammonium chloride, 18 parts of lauryl oleate, 16 parts of polyoxyethylene oleate, 4 parts of lauric acid diethanolamide, 4 parts of sodium dodecylbenzenesulfonate, 1.5 parts of octyl phosphate, 22 parts of lauryl oleate, 6007 parts of polyethylene glycol, 26 parts of dimethyl siloxane, 5 parts of sodium polymethacrylate, 7 parts of dioctyl phthalate.
[0030] The preparation method of above-mentioned spinning oil agent, step is as follows:
[0031] (1) take each component according to parts by weight;
[0032] (2) Add lauryl oleate, polyoxyethylene oleate, octyl phosphate, lauryl oleate, polyethylene glycol 600 and dioctyl phthalate into the reaction kettle and heat to 76 ℃, stirring for 28 minutes;
[0033] (3) Add the remaining components to the mixture obtained in step (2), stir at 73° C. for 16 minutes under a vacuum of 0.04 MPa, then cool down to 48° C., and stir for 32 minute...
PUM
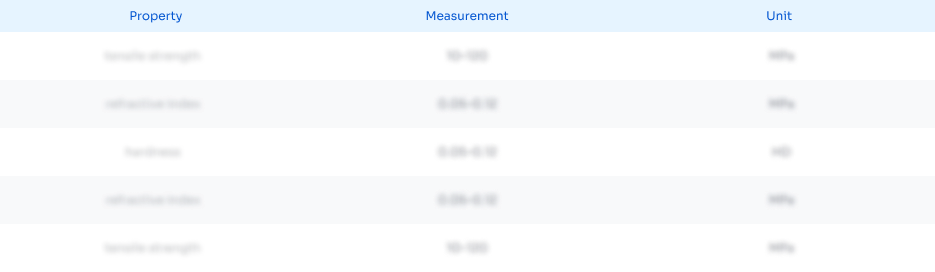
Abstract
Description
Claims
Application Information

- R&D
- Intellectual Property
- Life Sciences
- Materials
- Tech Scout
- Unparalleled Data Quality
- Higher Quality Content
- 60% Fewer Hallucinations
Browse by: Latest US Patents, China's latest patents, Technical Efficacy Thesaurus, Application Domain, Technology Topic, Popular Technical Reports.
© 2025 PatSnap. All rights reserved.Legal|Privacy policy|Modern Slavery Act Transparency Statement|Sitemap|About US| Contact US: help@patsnap.com