Method for using Ni-Co-W alloy electroplate liquid to repair nickel-plated combined crystallizer narrow plate in electroplating manner
An alloy electroplating solution, ni-co-w technology, applied in jewelry and other directions, can solve problems such as large repair volume, and achieve the effect of prolonging service life, novel concept and reducing processing volume
- Summary
- Abstract
- Description
- Claims
- Application Information
AI Technical Summary
Problems solved by technology
Method used
Image
Examples
Embodiment 1
[0026] The method for electroplating and repairing the nickel-plated combined crystallizer narrow plate with Ni-Co-W alloy electroplating solution is carried out according to the following steps:
[0027] The first step: configure the electrolyte
[0028] At room temperature, pour deionized water into the acid-resistant barrel, measure the calculated amount of sulfuric acid (the main component is hydrochloric acid, concentration 20% to 30%), sulfuric acid (98%), and add sulfuric acid and sulfuric acid along the wall of the acid-resistant barrel Add it to deionized water, stir while adding, the composition of the electrolyte is kokie acid: sulfuric acid: water = 1:1:6, let it cool for a certain period of time, and set it aside;
[0029] The second step: narrow plate rough machining
[0030] 1. Connect the tooling to the threaded hole on the back of the narrow plate with bolts, and then install and fix it on the machine table as a whole;
[0031] 2. Set the processing paramete...
Embodiment 2
[0043] The steps of this embodiment are the same as those of Embodiment 1, and the specific parameters are shown in Table 1.
Embodiment 3
[0045] The steps of this embodiment are the same as those of Embodiment 1, and the specific parameters are shown in Table 1.
[0046] Table 1 The method of electroplating and repairing the narrow plate of nickel-plated combined crystallizer with Ni-Co-W alloy electroplating solution
[0047] Specific parameters
[0048]
[0049] The method of the present invention carries out electroplating repair to the narrow copper plate of the crystallizer, and the working surface and the side of the narrow plate after electroplating are processed by the machine tool, and the phenomenon of peeling and shedding of the coating does not occur, and the effect of using the narrow plate on the line is the same as that of the previous coating structure. The use effect is the same, even better, and fully meets the production requirements.
PUM
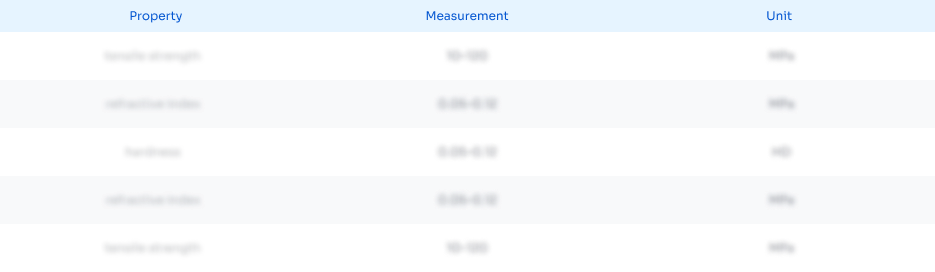
Abstract
Description
Claims
Application Information

- R&D
- Intellectual Property
- Life Sciences
- Materials
- Tech Scout
- Unparalleled Data Quality
- Higher Quality Content
- 60% Fewer Hallucinations
Browse by: Latest US Patents, China's latest patents, Technical Efficacy Thesaurus, Application Domain, Technology Topic, Popular Technical Reports.
© 2025 PatSnap. All rights reserved.Legal|Privacy policy|Modern Slavery Act Transparency Statement|Sitemap|About US| Contact US: help@patsnap.com