Integrated back board for high-reflectivity solar cells and manufacturing method thereof
A solar cell, high reflectivity technology, applied in final product manufacturing, sustainable manufacturing/processing, circuits, etc., can solve the problems of contaminating cells, reducing the amount of light on cells, reducing the photoelectric conversion efficiency of modules, etc. The effect of production efficiency
- Summary
- Abstract
- Description
- Claims
- Application Information
AI Technical Summary
Problems solved by technology
Method used
Examples
Embodiment 1
[0019] The adhesive is coated on both sides of the PET substrate with a thickness of 250 microns to form a bonding layer with a thickness of 10 microns, and the adhesive is baked and cured at 80-90°C for 10 minutes. Then heat-compress PVDF films with a thickness of 28 microns on the back of the PET at 110°C. Then, at 150°C, a 300-micron-thick polypropylene film containing 10% by mass fraction of titanium dioxide was hot-compressed on the front of the PET, and the size of the titanium dioxide was 300-400nm. Then, the EVA film with a thickness of 350 microns was hot-compressed on the surface of the polypropylene film at 110°C, cured at 60°C for 24 hours after winding, and an integrated high-reflectivity photovoltaic backplane was obtained after cooling.
Embodiment 2
[0021] The adhesive is coated on both sides of the PET substrate with a thickness of 180 microns to form a bonding layer with a thickness of 10 microns, and the adhesive is baked and cured at 80-90°C for 10 minutes. Then heat-compress a polyvinyl fluoride film with a thickness of 35 microns on the back of the PET at 80°C. Then, at 160°C, a polyolefin film with a thickness of 300 microns containing 10% by mass fraction of silicon dioxide was hot-compressed and laminated on the front of the PET, and the size of the silicon dioxide was 200nm. Then heat-compress the EVA film with a thickness of 300 microns on the surface of the polyolefin film at 110°C, roll it up and mature it at 60°C for 24 hours, and obtain an integrated high-reflectivity photovoltaic backplane after cooling.
Embodiment 3
[0023] The adhesive is coated on both sides of the PET substrate with a thickness of 180 microns to form a bonding layer with a thickness of 10 microns, and the adhesive is baked and cured at 80-90°C for 10 minutes. Then, a polyvinylidene fluoride film with a thickness of 30 microns is hot-pressed on the back of the PET at 110°C. Then, at 150°C, a polypropylene film with a thickness of 300 microns containing 10% by mass fraction of silica was hot-compressed and laminated on the front side of the PET, and the size of the silica was 200nm. Then heat-compress and compound a polyolefin film with a thickness of 350 microns on the surface of the polypropylene film at 110°C. After winding, it is aged at 60°C for 24 hours. After cooling, an integrated high-reflectivity photovoltaic backplane is obtained.
[0024] By adopting the above-mentioned integrated structure, the process of laying the lower encapsulating adhesive film in the production process of the module is reduced, and the ...
PUM
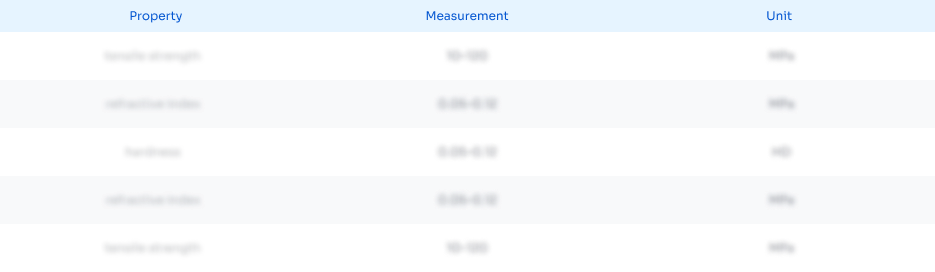
Abstract
Description
Claims
Application Information

- R&D Engineer
- R&D Manager
- IP Professional
- Industry Leading Data Capabilities
- Powerful AI technology
- Patent DNA Extraction
Browse by: Latest US Patents, China's latest patents, Technical Efficacy Thesaurus, Application Domain, Technology Topic, Popular Technical Reports.
© 2024 PatSnap. All rights reserved.Legal|Privacy policy|Modern Slavery Act Transparency Statement|Sitemap|About US| Contact US: help@patsnap.com