Method for machining TI-IGBT chip back structure
A processing method and technology of backside structure, applied in the field of microelectronics, can solve the problems of individual design and production of TI-IGBT chips, and achieve the effects of improving consistency, saving plate-making costs, and reducing production costs.
- Summary
- Abstract
- Description
- Claims
- Application Information
AI Technical Summary
Problems solved by technology
Method used
Image
Examples
Embodiment 1
[0035] In the embodiment of the present invention, an N-channel TI-IGBT is taken as an example, but it is also applicable to a P-channel TI-IGBT. It is only necessary to replace P / N with each other, which is the corresponding structure of P-channel TI-IGBT.
[0036] After the front process of the chip is completed, the back of the wafer is injected with P-type doping and then coated with photoresist on the back of the wafer. Then, according to the back mask plate, different areas are divided and exposed in sequence to form a back pattern;
[0037] The mask plate pattern contains a plurality of pattern units, and the pattern units are arranged symmetrically in translation; the relative position between the exposure areas is precisely controlled, so that the exposure pattern of the entire wafer is continuous and symmetrical in translation based on the pattern units; N-type doping is implanted on the back, and then the photoresist on the back is removed, and the back metallizati...
Embodiment 2
[0040] In addition, due to the lack of registration between the back graphics and the front graphics, it often results in a large (Nmax-Nmin) / (Nmax+Nmin), such as Figure 7The number of N+ collector regions contained on the back of chip A and chip B shown is quite different, and the parameter consistency for TI-IGBT is mainly related to the number of circular regions. If the number of N+ doped regions contained in different chips is very different (for example, the back of chip A contains 16 N+ doped regions, while the back of chip B only contains 9 N+ doped regions), it will inevitably lead to poor consistency of chip parameters .
[0041] see Figure 8 In order to reduce (Nmax-Nmin) / (Nmax+Nmin) as much as possible, an appropriate deflection angle can be formed between the arrangement direction of the graphic units on the back of the wafer and the arrangement direction of the chips on the front of the wafer. The calculation shows that (Nmax-Nmin) / (Nmax+Nmin) will change wit...
Embodiment 3
[0044] see Figure 10 , in order to further improve the consistency of parameters, the size of the chip can be matched with the cell size of the back pattern during design. Usually, chips with different voltages and current levels share the same back mask, that is to say, the size of the graphics unit on the back mask of the wafer is determined. In this way, the size of the chip on the front of the wafer is set as the unit of the graphics unit Integer multiples of the cell size. For the convenience of description, it is assumed that the graphics unit on the back of the wafer is a rectangle with a size of a×b. If the size of the chip is designed as ma×nb (m, n is a natural number), then although the graphics on the back are not aligned with the graphics on the front, the number of N+ collectors on the back of each chip is exactly the same, and the N+ collectors on the back of different chips The locations of the electrodes are exactly the same, which maximizes the consistency...
PUM
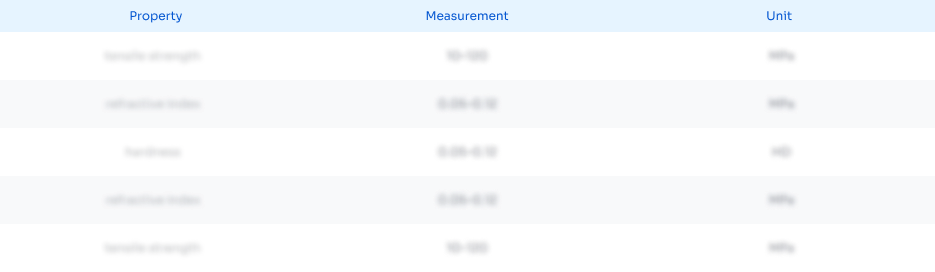
Abstract
Description
Claims
Application Information

- R&D
- Intellectual Property
- Life Sciences
- Materials
- Tech Scout
- Unparalleled Data Quality
- Higher Quality Content
- 60% Fewer Hallucinations
Browse by: Latest US Patents, China's latest patents, Technical Efficacy Thesaurus, Application Domain, Technology Topic, Popular Technical Reports.
© 2025 PatSnap. All rights reserved.Legal|Privacy policy|Modern Slavery Act Transparency Statement|Sitemap|About US| Contact US: help@patsnap.com