Graphene oxide sulfonate type waterborne polyurethane composite material and preparation method thereof
A technology of water-based polyurethane and olefin sulfonate, which is applied in the field of composite material preparation, can solve the problems of low heat resistance and achieve high heat resistance and good water dispersibility
- Summary
- Abstract
- Description
- Claims
- Application Information
AI Technical Summary
Problems solved by technology
Method used
Image
Examples
Embodiment 1
[0027] 1. Preparation of graphite oxide: In an ice bath, mix 4g of primary graphite powder, 4.8g of sodium nitrate and 160ml of concentrated sulfuric acid, and stir for 15 minutes to ensure thorough mixing, then slowly add 16g of potassium permanganate, and continue in the ice bath The reaction was stirred under conditions for 2 hours. Then it was stirred at room temperature for 36 hours. Slowly add 320ml of distilled water, stir for 15min, then add 320ml of distilled water to dilute, then add 40ml of 30wt% hydrogen peroxide to reduce the remaining potassium permanganate and MnO 2 , and finally the above reaction solution was repeatedly washed with deionized water until neutral, and then dried to obtain graphite oxide.
[0028] 2. Preparation of 1mg / ml graphene oxide aqueous dispersion: Take 0.25g of prepared graphite oxide and add it to 250ml of water, mix and stir evenly, and ultrasonically peel at 30°C for 1 hour to obtain 1mg / ml graphene oxide aqueous dispersion liquid. ...
Embodiment 2
[0031] 1. Preparation of graphite oxide: In an ice bath, mix 5g of primary graphite powder, 4g of sodium nitrate and 225ml of concentrated sulfuric acid, and stir for 20min to ensure thorough mixing, then slowly add 30g of potassium permanganate, and continue to mix in the ice bath The reaction was stirred for 2.5 hours. Then it was stirred at room temperature for 42 hours. Slowly add 450ml of distilled water, stir for 15min, then add 350ml of distilled water to dilute, then add 60ml of 30wt% hydrogen peroxide to reduce the remaining potassium permanganate and MnO 2 , and finally the above reaction solution was repeatedly washed with deionized water until neutral, and then dried to obtain graphite oxide.
[0032] 2. Preparation of 3 mg / ml graphene oxide aqueous dispersion: Take 0.75 g of the prepared graphite oxide and add it to 250 ml of water, mix and stir evenly, and ultrasonically peel at 30° C. for 1.5 hours to obtain a 3 mg / ml graphene oxide aqueous dispersion.
[0033...
Embodiment 3
[0035] 1. Preparation of graphite oxide: In an ice bath, mix 5g of primary graphite powder, 5g of sodium nitrate and 250ml of concentrated sulfuric acid, and stir for 30min to ensure thorough mixing, then slowly add 40g of potassium permanganate, and continue in the ice bath The reaction was stirred for 2.5 hours. Then the ice bath was removed, and stirred at room temperature for 48 hours. Slowly add 500ml of distilled water, stir for 15min, then add 250ml of distilled water to dilute, then add 75ml of 30wt% hydrogen peroxide to reduce the remaining potassium permanganate and MnO 2 , and finally the above reaction solution was repeatedly washed with deionized water until neutral, and then dried to obtain graphite oxide.
[0036] 2. Preparation of 5mg / ml graphene oxide aqueous dispersion: Take 1.25g of the prepared graphite oxide and add it to 250ml of water, mix and stir evenly, and ultrasonically peel at 30°C for 2 hours to obtain a 5mg / ml graphene oxide acetone dispersion. ...
PUM
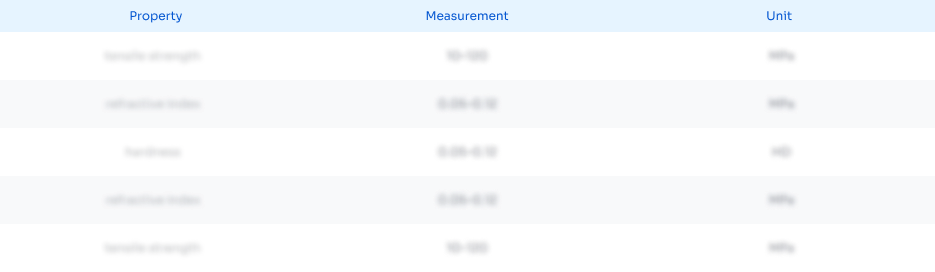
Abstract
Description
Claims
Application Information

- R&D
- Intellectual Property
- Life Sciences
- Materials
- Tech Scout
- Unparalleled Data Quality
- Higher Quality Content
- 60% Fewer Hallucinations
Browse by: Latest US Patents, China's latest patents, Technical Efficacy Thesaurus, Application Domain, Technology Topic, Popular Technical Reports.
© 2025 PatSnap. All rights reserved.Legal|Privacy policy|Modern Slavery Act Transparency Statement|Sitemap|About US| Contact US: help@patsnap.com