Double-S-bend infrared stealth spray pipe structure capable of achieving multi-direction thrust vector control
A technology of thrust vector control and multi-direction, which is applied to jet propulsion devices, machines/engines, etc., can solve the problems of only pitching thrust vector control or yaw thrust vector control, low reliability, large number, etc., to achieve easy Large-scale promotion and application, simple and reasonable structure, ingenious and novel ideas
- Summary
- Abstract
- Description
- Claims
- Application Information
AI Technical Summary
Problems solved by technology
Method used
Image
Examples
Embodiment Construction
[0020] The present invention can realize the double S-curved invisible nozzle structure of multi-directional thrust vector control, which is composed of double S-curved contracting nozzles, rectangular convergent-expanding nozzles and high-pressure secondary flow devices on the converging-expanding nozzles, refer to Figure 10 , the double S-curved contracting nozzle is composed of two S-shaped channels, the first S-shaped channel is deflected downward to make the airflow deviate from the axial direction of the engine, the second S-shaped channel is deflected upward to make the airflow return to the axial direction of the engine, and the two S-shaped channels are The ratio of the length of the S-shaped channel is selected at 2:3-2:5 to ensure the higher aerodynamic performance of the S-shaped nozzle, and the two S-shaped channels and the axial offset meet Figure 10 As shown in the condition of completely shielding the turbine, the two offset distances can be adjusted according...
PUM
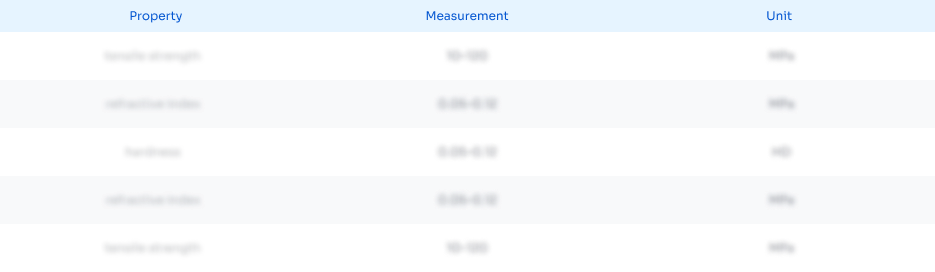
Abstract
Description
Claims
Application Information

- Generate Ideas
- Intellectual Property
- Life Sciences
- Materials
- Tech Scout
- Unparalleled Data Quality
- Higher Quality Content
- 60% Fewer Hallucinations
Browse by: Latest US Patents, China's latest patents, Technical Efficacy Thesaurus, Application Domain, Technology Topic, Popular Technical Reports.
© 2025 PatSnap. All rights reserved.Legal|Privacy policy|Modern Slavery Act Transparency Statement|Sitemap|About US| Contact US: help@patsnap.com