Production method for constant-section composite-material section material
A production method and technology of composite materials, which can be used in fabrics, textiles, textiles and papermaking, etc., can solve problems such as inability to meet complex load conditions, and achieve the effect of being suitable for large-scale promotion and use, with excellent performance and good bearing capacity.
- Summary
- Abstract
- Description
- Claims
- Application Information
AI Technical Summary
Problems solved by technology
Method used
Image
Examples
Embodiment Construction
[0026] The present invention will be further described below in conjunction with the embodiments and accompanying drawings.
[0027] A kind of production method (abbreviation production method of the equal cross-section composite profile of the present invention's design, see Figure 1-6 ), the production method adopts the following process steps:
[0028] 1) Weaving process: a large-scale 2.5D three-dimensional loom is used to arrange multi-layer warp yarns at equal intervals, and the manufacturing of 2.5D prefabricated fabrics on-line three-dimensional fabrics is completed through the processes of warping, drafting, shedding, weft insertion and weft beating; the multi-layer The warp yarn is at least one of carbon fiber, glass fiber, quartz fiber, aramid fiber or basalt fiber;
[0029] 2) Pre-setting process: the 2.5D structured three-dimensional fabric completed by the weaving process is transferred to the pre-setting device through the transmission device, and the pre-fabr...
PUM
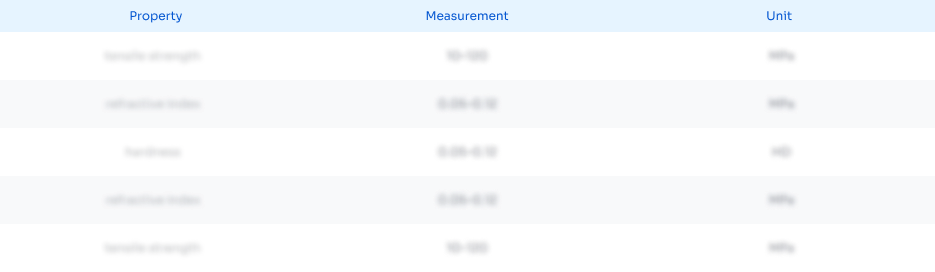
Abstract
Description
Claims
Application Information

- R&D
- Intellectual Property
- Life Sciences
- Materials
- Tech Scout
- Unparalleled Data Quality
- Higher Quality Content
- 60% Fewer Hallucinations
Browse by: Latest US Patents, China's latest patents, Technical Efficacy Thesaurus, Application Domain, Technology Topic, Popular Technical Reports.
© 2025 PatSnap. All rights reserved.Legal|Privacy policy|Modern Slavery Act Transparency Statement|Sitemap|About US| Contact US: help@patsnap.com