Method for manufacturing brake disc, support bell for brake disc and brake disc
A bell-shaped, brake band technology, applied in the direction of brake components, brake discs, brake types, etc., to solve problems such as increasing storage and transportation volume and weight
- Summary
- Abstract
- Description
- Claims
- Application Information
AI Technical Summary
Problems solved by technology
Method used
Image
Examples
Embodiment Construction
[0046] With reference to the accompanying drawings, a composite brake disc is fully indicated with reference numeral 1 and comprises a bell 2 made of a first material, preferably sheet metal, in particular steel or aluminum alloy, and comprises Brake band 3 made of a second material, eg cast iron, aluminum alloy or fiber reinforced ceramic material.
[0047] The bell 2 has a connection 7 for connecting the brake disc 1 to the hub of the vehicle and a coupling 8 for connecting the bell 2 to the brake band 3 . The connecting portion 7 of the bell 2 is shaped as a cup having a tubular side wall 4 substantially coaxial with the axis of rotation (generally the axis of symmetry) 5 of the brake disc 1 and having transverse to the side wall 4 and preferably The bottom wall 6 is substantially perpendicular to the axis of rotation 5 . A coupling portion 8 is generally formed at the end of the side wall 4 opposite to the bottom wall 6 .
[0048] Brake band 3 ( Figure 3A to Figure 3C ...
PUM
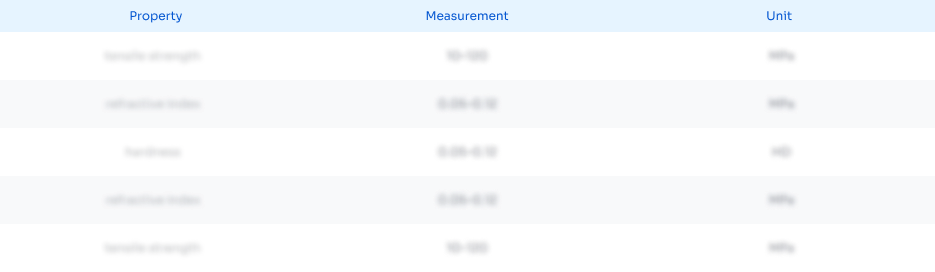
Abstract
Description
Claims
Application Information

- Generate Ideas
- Intellectual Property
- Life Sciences
- Materials
- Tech Scout
- Unparalleled Data Quality
- Higher Quality Content
- 60% Fewer Hallucinations
Browse by: Latest US Patents, China's latest patents, Technical Efficacy Thesaurus, Application Domain, Technology Topic, Popular Technical Reports.
© 2025 PatSnap. All rights reserved.Legal|Privacy policy|Modern Slavery Act Transparency Statement|Sitemap|About US| Contact US: help@patsnap.com