A processing method for grain refinement of crnimov high pressure steel forgings
A technology of grain refinement and processing method, applied in the direction of improving process efficiency, can solve the problems of grass wave, grain size difference, performance difference, etc., and achieve fine grain size, economical production process and production efficiency. high effect
- Summary
- Abstract
- Description
- Claims
- Application Information
AI Technical Summary
Problems solved by technology
Method used
Image
Examples
Embodiment Construction
[0026] A processing method for grain refinement of a CrNiMoV high-pressure steel forging, taking a 5-cylinder high-pressure steel forging as an example, the processing steps are as follows:
[0027] Step S01: Select grade-2 and 1000kg or above grade-2 steel scrap, nickel scrap, steel shavings, nickel-containing pig iron and sponge iron as electroslag ingots, use φ880 / φ940 crystallizers, and control the content of each element: C is 0.31 ~0.35%, Si 0.15~0.30%, Mn 0.50~0.65%, Ni 3.00~3.10%, Cr 0.90~1.00%, Mo 0.45~0.52%, Al 0.02~0.05%, V 0.05~ 0.10%, P not more than 0.015%, S not more than 0.010%, the five harmful elements Pb, As, Sn, Sb, and Bi are all less than 0.02%, and the amount of each element in the gas content is: [H] not more than 2.0ppm , [O] not greater than 30ppm, [N] not greater than 150ppm;
[0028] Step S02: heating the material selected in step S01 before forging to a temperature range of 1180-1210°C, and keeping it warm for 15 hours in this temperature range to...
PUM
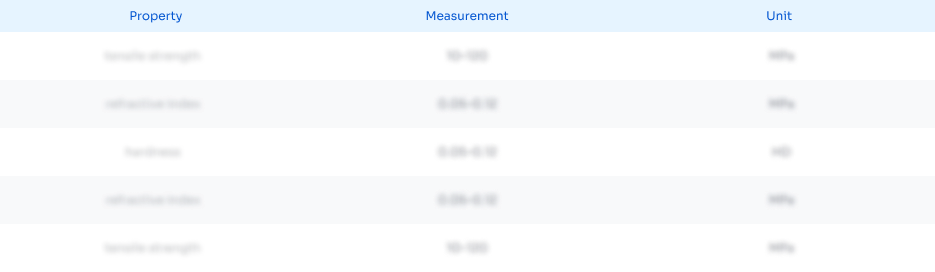
Abstract
Description
Claims
Application Information

- R&D
- Intellectual Property
- Life Sciences
- Materials
- Tech Scout
- Unparalleled Data Quality
- Higher Quality Content
- 60% Fewer Hallucinations
Browse by: Latest US Patents, China's latest patents, Technical Efficacy Thesaurus, Application Domain, Technology Topic, Popular Technical Reports.
© 2025 PatSnap. All rights reserved.Legal|Privacy policy|Modern Slavery Act Transparency Statement|Sitemap|About US| Contact US: help@patsnap.com