Piezoresistive type high overload microelectromechanical system (MEMS) accelerometer
An accelerometer and high-overload technology, applied in the direction of acceleration measurement using inertial force, impedance network, piezoelectric/electrostrictive/magnetostrictive devices, etc., can solve the deformation interference of the double-beam structure laterally, and the silicon chip bonding process Difficulties, difficulty in mass production, etc., to achieve the effect of improving sensitivity, large deformation, and low-cost mass production
- Summary
- Abstract
- Description
- Claims
- Application Information
AI Technical Summary
Problems solved by technology
Method used
Image
Examples
Embodiment Construction
[0033] The present invention will be further described below in conjunction with the accompanying drawings.
[0034] Such as Figure 3 to Figure 6 As shown, a piezoresistive MEMS high-overload accelerometer includes a square frame 4, 4 main beams 1, 4 microbeams 2 and a quality block 3; the main beam 1 is located in the square frame 4, and all The main beam 1 is connected to the mass block 3; the microbeam 2 is arranged on one side of the main beam 1, and the microbeam 2 is connected in parallel with the main beam 1, and the whole accelerometer structure is centrally symmetrical; the connection between the microbeam 2 and the main beam 1 A groove 9 is provided between them, and a buffer block 8 is respectively provided at the connection between the micro-beam 2 and the mass block 3 and the frame 4. The side of the buffer block 8 is a right-angled trapezoid, and the groove 9 causes the buffer block 8 to be separated from the main beam 1; The thickness of the buffer block 8 is ...
PUM
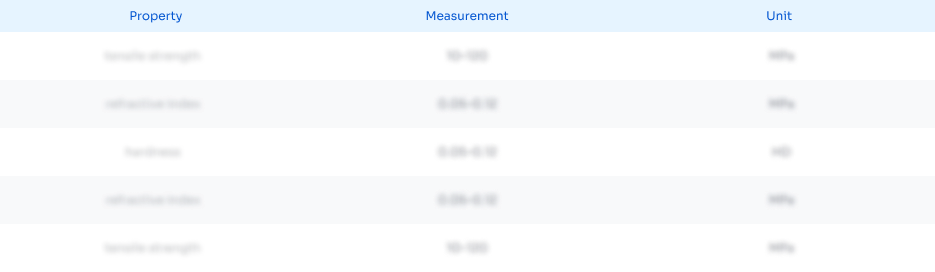
Abstract
Description
Claims
Application Information

- R&D Engineer
- R&D Manager
- IP Professional
- Industry Leading Data Capabilities
- Powerful AI technology
- Patent DNA Extraction
Browse by: Latest US Patents, China's latest patents, Technical Efficacy Thesaurus, Application Domain, Technology Topic, Popular Technical Reports.
© 2024 PatSnap. All rights reserved.Legal|Privacy policy|Modern Slavery Act Transparency Statement|Sitemap|About US| Contact US: help@patsnap.com