Test method for simulating corrosion process of aluminum alloy in salt-rich salt lake in atmospheric environment
A technology of atmospheric environment and corrosion process, applied in the direction of weather resistance/light resistance/corrosion resistance, measuring devices, instruments, etc., it can solve the problems such as the inability to simulate the atmospheric corrosion behavior of aluminum alloys well, and the accelerated research of aluminum alloy simulation, and achieve the Simulation, rapid evaluation and prediction, reproducible effect
- Summary
- Abstract
- Description
- Claims
- Application Information
AI Technical Summary
Problems solved by technology
Method used
Image
Examples
Embodiment 1
[0032] Aluminum alloy AA2024-T3 is used as the test material, and salt lake water is used as the corrosion medium, and an aerosol generator is used to deposit salt solution droplets on the surface of the sample until the solid deposition amount after evaporation of water on the surface of the sample is 100 μg / cm 2 , deposited on the surface of the sample once every three days; then proceed alternately according to "wet→dry", and cycle every 3 hours, wherein: in each cycle, the temperature of the wetting process is 30°C, and the wetting time is 1 hour (relatively within 1 hour The humidity increases linearly from 20% to 80%); the drying process temperature is 40°C, and the drying time is 2 hours (the relative humidity decreases linearly from 80% to 20% within 2 hours); the test time is 3 days. Corrosion products and pitting pits are evenly dispersed on the surface of the sample. At this time, the pitting pits are small and the corrosion products are not connected to each other (...
Embodiment 2
[0034] Aluminum alloy AA2024-T3 is used as the test material, and salt lake water is used as the corrosion medium, and an aerosol generator is used to deposit salt solution droplets on the surface of the sample until the solid deposition amount after evaporation of water on the surface of the sample is 100 μg / cm 2 , deposited on the surface of the sample once every three days; then proceed alternately according to "wet→dry", and cycle every 3 hours, wherein: in each cycle, the temperature of the wetting process is 30°C, and the wetting time is 1 hour (within 1 hour The relative humidity increases linearly from 20% to 80%); the drying process temperature is 40°C, and the drying time is 2 hours (the relative humidity decreases linearly from 80% to 20% within 2 hours); the test time is 9 days. The surface of the sample is covered with more crack-like corrosion products and pits, the pits become larger, and the interval corrosion products begin to connect together ( image 3 (b))....
Embodiment 3
[0036] Aluminum alloy AA2024-T3 is used as the test material, and salt lake water is used as the corrosion medium, and an aerosol generator is used to deposit salt solution droplets on the surface of the sample until the solid deposition amount after evaporation of water on the surface of the sample is 100 μg / cm 2 , deposited on the surface of the sample once every three days; then proceed alternately according to "wet→dry", and cycle every 3 hours, wherein: in each cycle, the temperature of the wetting process is 30°C, and the wetting time is 1 hour (within 1 hour The relative humidity increases linearly from 20% to 80%); the drying process temperature is 40°C, and the drying time is 2 hours (the relative humidity decreases linearly from 80% to 20% within 2 hours); the test time is 15 days.
[0037] At this time, the corrosion product layer on the surface of the sample is thicker, and the area of the pitting pit is larger ( image 3 (c)). The cross-sectional morphology sho...
PUM
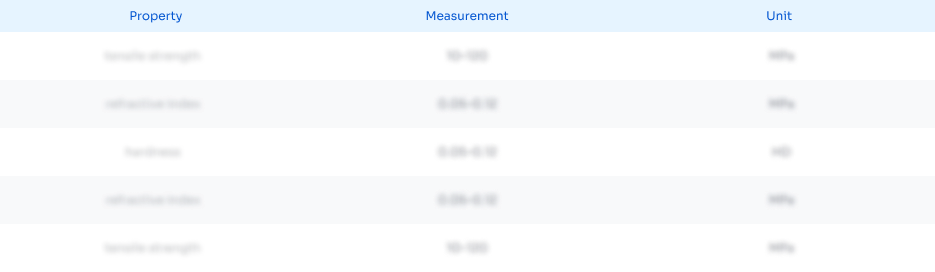
Abstract
Description
Claims
Application Information

- R&D Engineer
- R&D Manager
- IP Professional
- Industry Leading Data Capabilities
- Powerful AI technology
- Patent DNA Extraction
Browse by: Latest US Patents, China's latest patents, Technical Efficacy Thesaurus, Application Domain, Technology Topic, Popular Technical Reports.
© 2024 PatSnap. All rights reserved.Legal|Privacy policy|Modern Slavery Act Transparency Statement|Sitemap|About US| Contact US: help@patsnap.com