Method for producing high-purity sodium sulfite and sodium sulfate by desulfurizing coal-fired flue gas through alkaline method
A technology of coal-fired flue gas and sodium sulfite, which is applied in the field of coal-fired flue gas desulfurization, can solve the problems of unsolved by-product use, large cost enterprises, and high operating costs, achieve significant technical and economic effects, solve secondary pollution, and reduce desulfurization. burden effect
- Summary
- Abstract
- Description
- Claims
- Application Information
AI Technical Summary
Problems solved by technology
Method used
Examples
Embodiment 1
[0016] A method for producing high-purity sodium sulfite and sodium sulfate through alkaline desulfurization of coal-fired flue gas, the steps are as follows:
[0017] 1) First stage desulfurization
[0018] In the desulfurization tower, the coal-fired flue gas is fed into the bottom, and the desulfurization liquid is sprayed on the upper part. The gas flow rate of the coal-fired flue gas is 30m / s. The liquid mass is 2wt% sodium thiosulfate, the amount ratio of desulfurization liquid to coal-fired flue gas is 3L / m3, the desulfurization temperature is 95°C, and when the pH value of the desulfurization liquid is 1.8, the desulfurization liquid is released and filtered with 32wt% Adjust the pH of the sodium hydroxide solution to 6.5, enter the evaporator to evaporate, and transfer it to the cooler when it evaporates to crystallization, cool to 20°C, separate the crystallization with a centrifuge, and obtain sodium sulfate after drying. The sodium sulfate content is 95.5 %, the r...
Embodiment 2
[0022] A method for producing high-purity sodium sulfite and sodium sulfate through alkaline desulfurization of coal-fired flue gas, the steps are as follows:
[0023] 1) First stage desulfurization
[0024] In the desulfurization tower, the coal-fired flue gas is fed into the bottom, and the desulfurization liquid is sprayed on the upper part. The gas flow rate of the coal-fired flue gas is 30m / s. 1wt% bisphenol A in liquid mass, the dosage ratio of desulfurization liquid to coal-fired flue gas is 3L / m3, the desulfurization temperature is 95°C, and when the pH value of the desulfurization liquid is 2.0, release the desulfurization liquid, filter and use 32wt% bisphenol A The sodium hydroxide solution adjusts the pH to 6.8, enters the evaporator to evaporate, transfers to the cooler when it evaporates to crystallization, cools to 20°C, separates the crystallization with a centrifuge, and obtains sodium sulfate after drying. The sodium sulfate content is 96.3%. , the mother li...
Embodiment 3
[0028] A method for producing high-purity sodium sulfite and sodium sulfate through alkaline desulfurization of coal-fired flue gas, the steps are as follows:
[0029] 1) First stage desulfurization
[0030] In the desulfurization tower, the coal-fired flue gas is fed into the bottom, and the desulfurization liquid is sprayed on the upper part. The gas flow rate of the coal-fired flue gas is 30m / s. The liquid mass is 1.2wt% hydroquinone, the dosage ratio of desulfurization liquid to coal-fired flue gas is 3L / m3, the desulfurization temperature is 95°C, and when the pH value of the desulfurization liquid is 2.0, the desulfurization liquid is released and filtered with 32wt % sodium hydroxide solution to adjust the pH to 6.9, enter the evaporator to evaporate, transfer to the cooler when crystallization occurs after evaporation, cool to 20°C, separate the crystallization with a centrifuge, and obtain sodium sulfate after drying. The sodium sulfate content is detected as 95.8%, ...
PUM
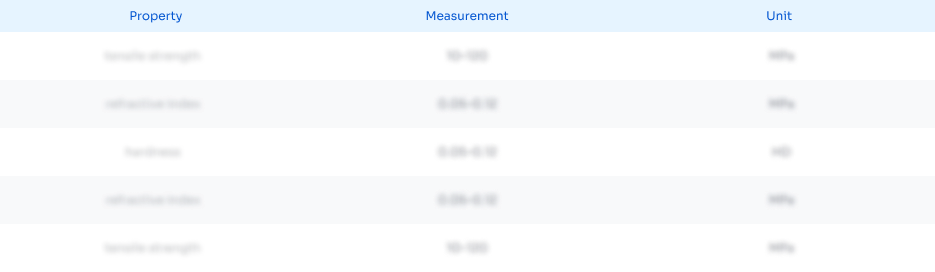
Abstract
Description
Claims
Application Information

- R&D
- Intellectual Property
- Life Sciences
- Materials
- Tech Scout
- Unparalleled Data Quality
- Higher Quality Content
- 60% Fewer Hallucinations
Browse by: Latest US Patents, China's latest patents, Technical Efficacy Thesaurus, Application Domain, Technology Topic, Popular Technical Reports.
© 2025 PatSnap. All rights reserved.Legal|Privacy policy|Modern Slavery Act Transparency Statement|Sitemap|About US| Contact US: help@patsnap.com