Method for recycling titanium, silicon, aluminum, calcium and magnesium from titaniferous blast furnace slag by multistage acid leaching
A technology for acid leaching and blast furnace slag, which is applied in the fields of magnesium, silicon, ironmaking or steelmaking process, manganese and iron, calcium, vanadium, chromium, aluminum, and titanium recovery
- Summary
- Abstract
- Description
- Claims
- Application Information
AI Technical Summary
Problems solved by technology
Method used
Examples
Embodiment 1
[0110] 1), smash
[0111] Titanium-containing blast furnace slag (water-quenched slag TiO 2 : 23.94%, CaO: 25.08%, SiO 2 : 24.06%, MgO: 8.05%, Al2O3: 17.95%, other about 1%) magnetic separation, dry crushing to 325 mesh.
[0112] 2), Concentrated acid leaching, oxidation and leaching slag washing
[0113] 2.1), one-stage acid leaching and leaching residue washing
[0114] In a 500ml three-necked flask, add 300ml of concentrated hydrochloric acid (Cl: 406g / l, H: 11.50g / l) with a concentration greater than 34%, start stirring, add 20g of blast furnace slag powder, heat up to 68-72°C, and strictly control Below 73°C, wait for the material liquid to become transparent and change from thick to thin, keep the temperature and stir for 0.5 hours, then the reaction is qualified. Suction filtration, get filtrate 260ml (Cl: 406g / l, H: 9.28g / l, Mg: 3.25g / l, Ca: 11.95g / l, Al: 6.35g / l, Ti: 7.68g / l, Fe: 0.43g / l, V: 0.18g / l, Cr: 0.15g / l, Mn: 0.37g / l) for two-stage acid leaching; :2 hydr...
Embodiment 2
[0162] 1), smash
[0163] Titanium-containing blast furnace slag (water-quenched slag TiO 2 : 14.04%, CaO: 28.07%, SiO 2 : 24.26%, MgO: 11.97%, Al 2 o 3 : 21.03%, other about 1%) magnetic separation, dry crushing to 325 mesh.
[0164] 2), Concentrated acid leaching, oxidation and leaching slag washing
[0165] 2.1), one-stage acid leaching and leaching residue washing
[0166] In a 500ml three-necked flask, add 300ml of concentrated hydrochloric acid (Cl: 410.45g / l, H: 11.52g / l) with a concentration greater than 34%, start stirring, add 20g of blast furnace slag powder, heat up to 68-72°C, strictly control Below 73°C, when the material liquid becomes transparent and changes from thick to thin, keep the temperature and stir for 0.5 hours to pass the reaction. Suction filtration, get filtrate 260ml (Cl: 410.45g / l, H: 9.28g / l, Mg: 4.85g / l, Ca: 13.45g / l, Al: 7.25g / l, Ti: 4.06g / l, Fe : 0.38g / l, V: 0.10g / l, Cr: 0.15g / l, Mn: 0.41g / l) for two-stage acid leaching; Wash with 1:2...
Embodiment 3
[0211] Embodiment 3: (solid / liquid ratio is 1:20)
[0212] Example 1 was repeated, except that the four-stage acid leaching process was adopted.
[0213] 2. Four-stage acid leaching
[0214] 2.1 One-stage acid leaching and leaching residue washing
[0215] In a 500ml three-neck flask, add 300ml of concentrated hydrochloric acid (Cl: 406g / l, H: 11.50g / l) with a concentration greater than 34%, start stirring, add 15g of titanium-containing blast furnace slag powder, and control the temperature to 68-72°C. Strictly control the temperature below 73°C. After the material liquid becomes transparent and changes from thick to thin, keep the temperature and stir for 0.5 hours, then the reaction is qualified. Suction filtration, get filtrate 260ml (Cl: 406g / l, H: 9.28g / l, Mg: 3.25g / l, Ca: 11.95g / l, Al: 6.35g / l, Ti: 7.68g / l, Fe: 0.43g / l, V: 0.18g / l, Cr: 0.15g / l, Mn: 0.37g / l) for two-stage acid leaching; :2 hydrochloric acid, 1:5, 1:10 dilute hydrochloric acid, tap water washed, dried...
PUM
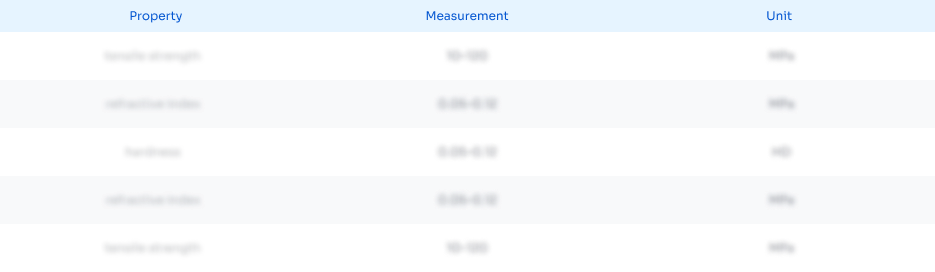
Abstract
Description
Claims
Application Information

- R&D
- Intellectual Property
- Life Sciences
- Materials
- Tech Scout
- Unparalleled Data Quality
- Higher Quality Content
- 60% Fewer Hallucinations
Browse by: Latest US Patents, China's latest patents, Technical Efficacy Thesaurus, Application Domain, Technology Topic, Popular Technical Reports.
© 2025 PatSnap. All rights reserved.Legal|Privacy policy|Modern Slavery Act Transparency Statement|Sitemap|About US| Contact US: help@patsnap.com