Hydraulic double-motor driving electronic hydraulic braking system
A dual-motor drive, hydraulic braking technology, applied in brakes, brake transmissions, transportation and packaging, etc., can solve problems such as hidden dangers in reliability and safety, inability to guarantee pedal feel, and insufficient use of manpower. Guaranteed brake pedal feel, reduced motor power, and fast response
- Summary
- Abstract
- Description
- Claims
- Application Information
AI Technical Summary
Problems solved by technology
Method used
Image
Examples
Embodiment Construction
[0031] The present invention will be further described below in conjunction with the examples shown in the accompanying drawings.
[0032] Such as figure 1 As shown, the hydraulic dual-motor driven electronic hydraulic braking system mainly includes a brake pedal 1, a first electronically controlled linear motion module 28, a second electronically controlled linear motion module 29, a brake master cylinder 11, and a secondary master cylinder 23 , solenoid valve 14, solenoid valve 15, solenoid valve 16, solenoid valve 17, pedal displacement sensor 12, hydraulic pressure sensor 18, ESC module 27, liquid storage tank 4, electronic control unit 30 and control lines 33, 34, 35, 36 , 37. The first electronically controlled linear motion module 28 and the second electronically controlled linear motion module 29 include a motor and a motion adjustment mechanism. The motion adjustment mechanism of the first electronically controlled linear motion module is connected to the brake pedal...
PUM
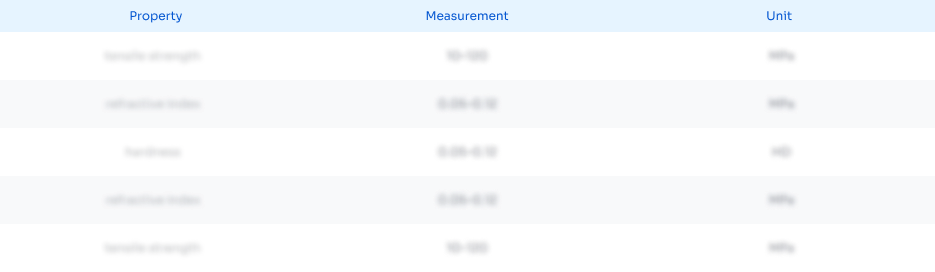
Abstract
Description
Claims
Application Information

- R&D Engineer
- R&D Manager
- IP Professional
- Industry Leading Data Capabilities
- Powerful AI technology
- Patent DNA Extraction
Browse by: Latest US Patents, China's latest patents, Technical Efficacy Thesaurus, Application Domain, Technology Topic, Popular Technical Reports.
© 2024 PatSnap. All rights reserved.Legal|Privacy policy|Modern Slavery Act Transparency Statement|Sitemap|About US| Contact US: help@patsnap.com