Catalyst for production of methacrylic acid and method for producing methacrylic acid using same
A technology of methacrylic acid and methacrolein, applied in the direction of catalyst activation/preparation, heterogeneous catalyst chemical elements, organic chemical methods, etc., can solve the problems of high hygroscopicity, catalyst performance degradation, and improve activity, etc., to achieve moisture absorption excellent effect
- Summary
- Abstract
- Description
- Claims
- Application Information
AI Technical Summary
Problems solved by technology
Method used
Image
Examples
Embodiment 1
[0069] 1) Preparation of catalyst
[0070] 800 g of molybdenum trioxide, 40.43 g of vanadium pentoxide, and 73.67 g of 85% by mass orthophosphoric acid were added to 5680 ml of pure water, and heated and stirred at 92° C. for 3 hours to obtain a reddish-brown transparent solution. Next, the solution was cooled to 15-20° C., 307.9 g of a 9.1 mass % cesium hydroxide aqueous solution and 689.0 g of a 14.3 mass % ammonium acetate aqueous solution were slowly added while stirring, and aged at 15-20° C. for 1 hour to obtain Yellow paste. Next, 709.9 g of 6.3 mass % copper acetate aqueous solution was further slowly added to this slurry, and it aged at 15-20 degreeC for 30 minutes further. Next, this slurry was spray-dried to obtain granules. The composition of the obtained particles is Mo 10 V 0.8 P 1.15 Cu 0.4 Cs 0.3 (NH 4 ) 2.3 . 320 g of the pellets were calcined at 310° C. for 5 hours under air circulation to obtain precalcined pellets. The mass was reduced by about 4...
Embodiment 2
[0077] A coated catalyst was prepared in the same manner as in Example 1 except that the precalcination temperature was set to 290° C. in Example 1. The composition of the obtained catalyst is Mo 10 V 0.8 P 1.15 Cu 0.4 Cs 0.3 (NH 4 ) 2.3 Sb 1.0 . The methacrolein oxidation reaction and the moisture absorption measurement were carried out in the same manner as in Example 1 except that the coated catalyst was used. The results are shown in Table 1 and Table 2.
Embodiment 3
[0079] A coated catalyst was prepared in the same manner as in Example 1, except that 320 g of precalcined particles, 11.35 g of antimony trioxide, and 45 g of a strength improving agent (ceramic fiber) were uniformly mixed in Example 1. The composition of the obtained catalyst is Mo 10 V 0.8 P 1.15 Cu 0.4 Cs 0.3 (NH 4 ) 2.3 Sb 0.5 . In addition, at this time, α=1.1. The methacrolein oxidation reaction and the moisture absorption measurement were carried out in the same manner as in Example 1 except that the coated catalyst was used. The results are shown in Table 1 and Table 2.
PUM
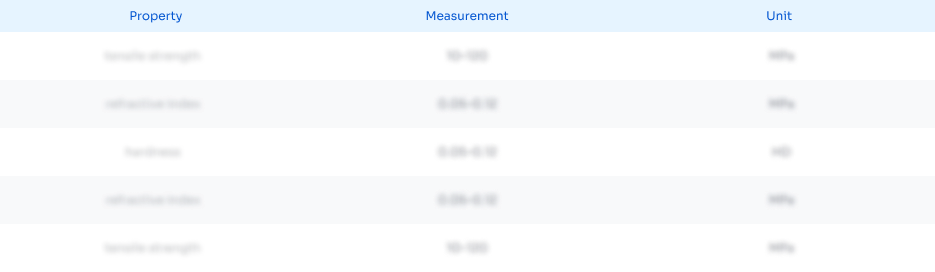
Abstract
Description
Claims
Application Information

- R&D
- Intellectual Property
- Life Sciences
- Materials
- Tech Scout
- Unparalleled Data Quality
- Higher Quality Content
- 60% Fewer Hallucinations
Browse by: Latest US Patents, China's latest patents, Technical Efficacy Thesaurus, Application Domain, Technology Topic, Popular Technical Reports.
© 2025 PatSnap. All rights reserved.Legal|Privacy policy|Modern Slavery Act Transparency Statement|Sitemap|About US| Contact US: help@patsnap.com