Remote monitoring system and method for fatigue cracks of orthotropic steel bridge deck slab
A steel bridge deck, orthotropic technology, applied in transmission systems, measuring devices, material analysis through optical means, etc., can solve the problem of inability to reach sensitive areas of fatigue cracking, inability to accurately determine the position of the crack tip, and areas inaccessible to the operating space and other issues, to achieve the effect of convenient and flexible placement, simplifying the monitoring workload, and satisfying multi-point monitoring
- Summary
- Abstract
- Description
- Claims
- Application Information
AI Technical Summary
Problems solved by technology
Method used
Image
Examples
Embodiment Construction
[0036] The present invention will be described in detail below in conjunction with specific embodiments. The following examples will help those skilled in the art to further understand the present invention, but do not limit the present invention in any form. It should be noted that those skilled in the art can make several modifications and improvements without departing from the concept of the present invention. These all belong to the protection scope of the present invention.
[0037] Such as Figure 1-5 As shown, this embodiment provides a remote monitoring system for fatigue cracks of orthotropic steel bridge decks, including an in-situ detection device 1, a wireless gateway 2 and a remote control device 3, wherein:
[0038] The in-situ detection device 1 is composed of break line components 4, 4-1...4-n, path detectors 5, 5-1...5-n and wireless terminals 6, 6-1...6-n; The breakage line components 4, 4-1...4-n are composed of optical fibers or resistance breakage line...
PUM
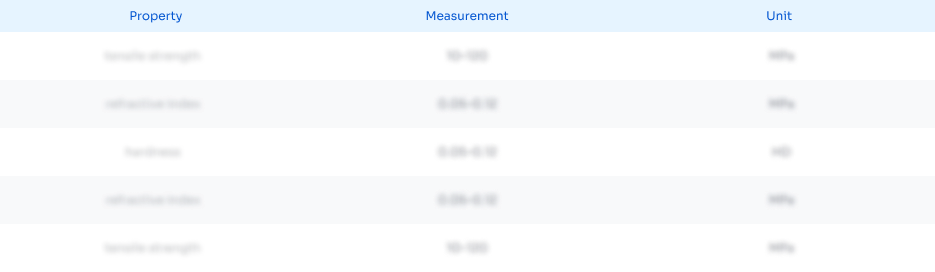
Abstract
Description
Claims
Application Information

- R&D Engineer
- R&D Manager
- IP Professional
- Industry Leading Data Capabilities
- Powerful AI technology
- Patent DNA Extraction
Browse by: Latest US Patents, China's latest patents, Technical Efficacy Thesaurus, Application Domain, Technology Topic, Popular Technical Reports.
© 2024 PatSnap. All rights reserved.Legal|Privacy policy|Modern Slavery Act Transparency Statement|Sitemap|About US| Contact US: help@patsnap.com