Gas intake system and substrate processing equipment
A technology of air intake system and air inlet, applied in the field of microelectronics, can solve the problems of low efficiency, limited shortening of the intake pipeline 20, and long exhaust time of residual gas, so as to improve process efficiency, shorten exhaust time, The effect of improving efficiency
- Summary
- Abstract
- Description
- Claims
- Application Information
AI Technical Summary
Problems solved by technology
Method used
Image
Examples
Embodiment Construction
[0031] In order for those skilled in the art to better understand the technical solutions of the present invention, the air intake system and substrate processing equipment provided by the present invention will be described in detail below with reference to the accompanying drawings.
[0032] figure 2 The schematic diagram of the air intake system provided by the first embodiment of the present invention. see figure 2The air intake system includes an air inlet connected to the reaction chamber, an air intake pipeline, an exhaust pump 35 and at least one gas source, and the gas types of different gas sources are different. Wherein, the gas inlet can be a gas nozzle, a through hole, etc., which can communicate with the reaction chamber; the gas source includes at least one carrier gas source and at least one reaction gas source; the carrier gas refers to the The gas that does not physically or chemically interact with the substrate during the etching process and is used to ...
PUM
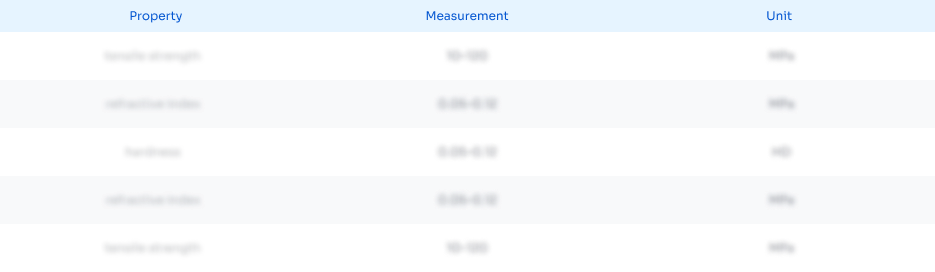
Abstract
Description
Claims
Application Information

- R&D Engineer
- R&D Manager
- IP Professional
- Industry Leading Data Capabilities
- Powerful AI technology
- Patent DNA Extraction
Browse by: Latest US Patents, China's latest patents, Technical Efficacy Thesaurus, Application Domain, Technology Topic, Popular Technical Reports.
© 2024 PatSnap. All rights reserved.Legal|Privacy policy|Modern Slavery Act Transparency Statement|Sitemap|About US| Contact US: help@patsnap.com