High bearing capacity composite material roller
A technology of composite materials and bearing columns, which is applied in the direction of bearing components, shafts and bearings, layered products, etc., can solve the problems of reduced bearing capacity, large plastic deformation, and high bearing strength
- Summary
- Abstract
- Description
- Claims
- Application Information
AI Technical Summary
Problems solved by technology
Method used
Image
Examples
Embodiment 1
[0010] Embodiment 1: (as figure 1 shown)
[0011] This embodiment is a hollow cylinder, which is composed of three layers of spring steel 1 with high relative hardness and high elasticity and polyurethane material 2 with low relative hardness and high elasticity. Both ends of the column are closed by spring steel to form a complete cylinder. The surface layer of spring steel is backed by two layers of inner lining materials that are both rigid and soft, and the column will deform to a certain extent under high loads, thereby increasing the surface contact bearing area correspondingly, and then greatly improving the bearing capacity.
Embodiment 2
[0012] Embodiment 2: (as figure 2 shown)
[0013] This embodiment is a hollow cylinder, which is composed of bearing steel 1 with high relative hardness and high elasticity and modified nylon material 2 with low relative hardness and high elasticity. Its carrying mechanism is the same as that in Embodiment 1. The difference is that bearing steel is harder and more brittle than spring steel. Place it inside the second and fourth floors. Modified nylon is used for the surface layer and the third layer. It has both toughness and elasticity. And better strength. Carry out optimized design and rational layout. The noise reduction effect of the roller in bearings and or other rotating mechanisms is very obvious.
Embodiment 3
[0014] Embodiment 3: (as image 3 shown)
[0015] This embodiment is a solid cylinder, which is composed of stainless steel 304 material 1 with high relative hardness and high elasticity, and basalt fiber with a network structure with low relative hardness and high elasticity and modified PP material molten mixture composite material 2. Composite. The interior is a fusion composite material of basalt fiber and modified PP material, and the composite material itself is a column with high compressive strength. The outer surface is sealed and wrapped with stainless steel 304 material with high hardness and high elasticity, which further improves its carrying capacity.
PUM
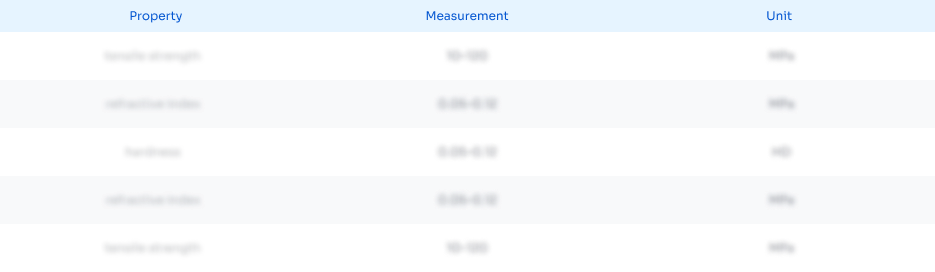
Abstract
Description
Claims
Application Information

- Generate Ideas
- Intellectual Property
- Life Sciences
- Materials
- Tech Scout
- Unparalleled Data Quality
- Higher Quality Content
- 60% Fewer Hallucinations
Browse by: Latest US Patents, China's latest patents, Technical Efficacy Thesaurus, Application Domain, Technology Topic, Popular Technical Reports.
© 2025 PatSnap. All rights reserved.Legal|Privacy policy|Modern Slavery Act Transparency Statement|Sitemap|About US| Contact US: help@patsnap.com