Inertial sensor production and wafer level package process based on MEMS (micro-electromechanical system)
A wafer-level packaging, inertial sensor technology, applied in the process of producing decorative surface effects, decorative arts, metal material coating processes, etc., can solve the problems of ASIC design space limitation, MEMS area waste, and high production costs, Achieve the effect of reducing production and testing costs, reducing packaging areas, and improving performance
- Summary
- Abstract
- Description
- Claims
- Application Information
AI Technical Summary
Problems solved by technology
Method used
Image
Examples
Embodiment Construction
[0038] In order to make the technical means, technical features, invention objectives and technical effects realized by the present invention easy to understand, the present invention will be further described below in conjunction with specific illustrations.
[0039] A production and wafer-level packaging process based on MEMS inertial sensors, see figure 1 , the steps are as follows:
[0040] 1) Engineered silicon-on-insulator formation (E-SOI):
[0041] a. Firstly use silicon to support the wafer (handle wafer) "5", etch the positioning alignment mark (the first photolithography plate) on the back, and then use the plasma process to etch the groove "1" (the second) on the front of the wafer. Photolithography); grow a layer of oxide film "7" by thermal oxidation process; bond with another MEMS wafer (Device wafer) "4" by silicon bonding process;
[0042] b. Grinding to the ideal thickness on the wafer surface of micro-electromechanical devices, such as figure 2 shown;
...
PUM
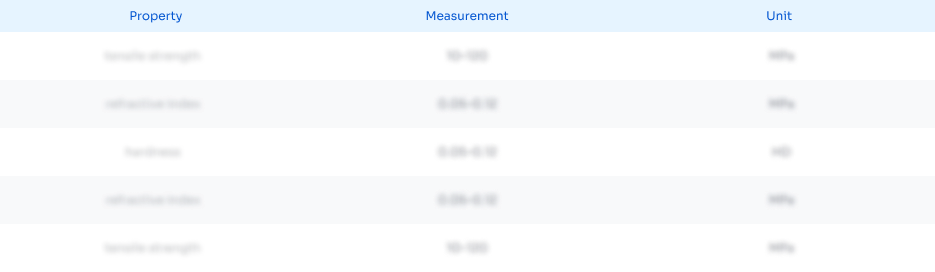
Abstract
Description
Claims
Application Information

- R&D Engineer
- R&D Manager
- IP Professional
- Industry Leading Data Capabilities
- Powerful AI technology
- Patent DNA Extraction
Browse by: Latest US Patents, China's latest patents, Technical Efficacy Thesaurus, Application Domain, Technology Topic, Popular Technical Reports.
© 2024 PatSnap. All rights reserved.Legal|Privacy policy|Modern Slavery Act Transparency Statement|Sitemap|About US| Contact US: help@patsnap.com