Composite filter material for heat-setting-free pleated filter cartridge and processing method of composite filter material
A composite filtration and processing method technology, applied in the field of filter materials, can solve the problems of high stiffness and mechanical folding yield, low production efficiency, poor folding yield, etc., to improve mechanical folding yield, improve production efficiency, mechanical folding good sex effect
- Summary
- Abstract
- Description
- Claims
- Application Information
AI Technical Summary
Problems solved by technology
Method used
Image
Examples
example 1
[0031] The plant fiber, synthetic fiber and glass fiber are respectively subjected to hydraulic dispersion and beating by a drum type hydraulic pulper under the condition of a pulp concentration of 1%, and the beating time is 8 minutes. After beating, mix according to the ratio of 20 parts of plant fiber, 10 parts of synthetic fiber and 70 parts of glass fiber, and mix it through a pulping machine to form a 2% concentration, which is now a mixture with water. At the same time, add 0.01% defoamer, 0.02% Dispersant, 0.2% compound antibacterial agent, to the slurry storage tank for slurry storage. After the mixed pulp is punched, it is sent to the headbox to be formed on the net, and the five dehydration zones of the wire part are dehydrated sequentially and gradually to keep the long fibers uniformly formed to form a fiber layer. Add 15% reinforcing adhesive to the wire part to strengthen, form and dehydrate through the wire part to form a wet paper tire with a dryness of 28%. T...
example 2
[0034] The plant fiber, synthetic fiber and glass fiber are respectively subjected to hydraulic dispersion and beating by a drum type hydraulic pulper under the condition of a pulp concentration of 1%, and the beating time is 8 minutes. After beating, mix according to the ratio of 30 parts of plant fiber, 5 parts of synthetic fiber and 65 parts of glass fiber, and mix it through a pulping machine to form a 2% concentration, which is now a mixture with water. At the same time, add 0.01% defoamer, 0.02% Dispersant, 0.2% compound antibacterial agent, to the slurry storage tank for slurry storage. After the mixed pulp is punched, it is sent to the headbox to be formed on the net, and at the same time, 3% composite flame retardant is added, and the five dehydration zones of the wire section are dehydrated sequentially in a gradient to keep the long fibers uniformly formed to form a fiber layer. Add 15% reinforcing adhesive to the wire part to strengthen, form and dehydrate through ...
example 3
[0037] The plant fiber, synthetic fiber and glass fiber are respectively subjected to hydraulic dispersion and beating by a drum type hydraulic pulper under the condition of a pulp concentration of 1%, and the beating time is 8 minutes. After beating, mix according to the ratio of 0 parts of plant fiber, 20 parts of synthetic fiber and 80 parts of glass fiber, and mix it through the pulping machine to form a 2% concentration, which is now a mixture with water. At the same time, add 0.01% defoamer, 0.02% Dispersant, 0.2% compound antibacterial agent, to the slurry storage tank for slurry storage. After the mixed pulp is punched, it is sent to the headbox to be formed on the net, and the five dehydration zones of the wire part are dehydrated sequentially and gradually to keep the long fibers uniformly formed to form a fiber layer. Add 15% reinforcing adhesive to the wire part to strengthen, form and dehydrate through the wire part to form a wet paper tire with a dryness of 28%. ...
PUM
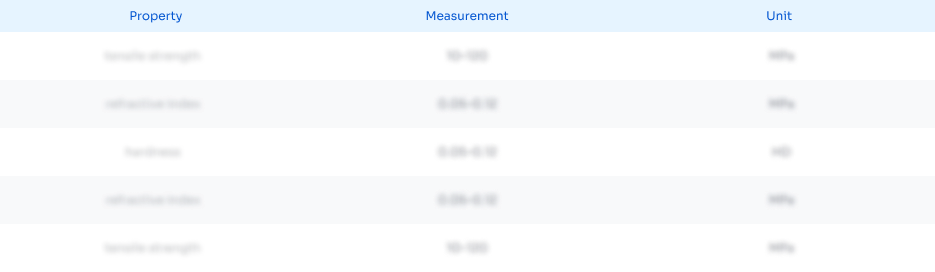
Abstract
Description
Claims
Application Information

- R&D
- Intellectual Property
- Life Sciences
- Materials
- Tech Scout
- Unparalleled Data Quality
- Higher Quality Content
- 60% Fewer Hallucinations
Browse by: Latest US Patents, China's latest patents, Technical Efficacy Thesaurus, Application Domain, Technology Topic, Popular Technical Reports.
© 2025 PatSnap. All rights reserved.Legal|Privacy policy|Modern Slavery Act Transparency Statement|Sitemap|About US| Contact US: help@patsnap.com