Polycarboxylate superplasticizer with high dispersion and high slump protection and preparation method of polycarboxylate superplasticizer
A technology of water reducing agent and polycarboxylic acid, which is applied in the field of polycarboxylate water reducing agent and its preparation, can solve the problems of reducing the adsorption of water reducing agent molecules and cement particles, affecting the conveying performance of concrete, and the same product performance, and improving the performance of the product. Workability, contact reduction, water consumption reduction effect
- Summary
- Abstract
- Description
- Claims
- Application Information
AI Technical Summary
Problems solved by technology
Method used
Image
Examples
Embodiment 1
[0053] Add allyl alcohol polyoxyethylene ether (MW=1100, 66.5g, see formula 1.1) into a 500mL four-necked flask equipped with mechanical stirring, temperature controller, and dripping device, and add deionized water (33.5g) at the same time, Heat up while stirring and dissolving; prepare the solution of monomer B and monomer C, that is, the solution of acrylic acid (12.97g, see formula 1.2) and 1-phenylacrylic acid (3.58g, see formula 1.3); prepare reducing agent and The solution of chain transfer agent, is about to ascorbic acid (0.12g), mercaptoacetic acid (0.27g) are dissolved in deionized water (52g); Preparation oxidizing agent solution, mass concentration is that 30% hydrogen peroxide (0.37g) is dissolved in deionized water (7.5g); when the temperature in the reaction bottle is 60~65°C, first add the oxidizing agent solution, after stirring for 5 minutes, then dropwise add the solution of monomer B and monomer C and the solution of reducing agent and chain transfer agent ...
Embodiment 2
[0057] Add methallyl alcohol polyoxyethylene ether (MW=2300, 139.05g, see formula 2.1) into a 500mL four-neck flask equipped with mechanical stirring, temperature controller, and dripping device, and add deionized water (71.63g ), heating up while stirring and dissolving; prepare a solution of monomer B and monomer C, that is, a solution of acrylic acid (13.08g, see formula 2.2) and 1-p-hydroxyphenylacrylic acid (3.57g, see formula 2.3); Prepare the solution of reducing agent and chain transfer agent, be about to dissolve ascorbic acid (0.09g), mercaptoacetic acid (0.18g) in deionized water (52g); prepare oxidizing agent solution, be that the mass concentration is 30% hydrogen peroxide (0.09g) dissolving In deionized water (7.5g); when the temperature in the reaction bottle is 60~65°C, first add the oxidizing agent solution, stir for 5 minutes, then dropwise add the solutions of monomer B and monomer C, reducing agent and chain transfer The solution of the agent was added drop...
Embodiment 3
[0061] Add allyl alcohol polyoxyethylene ether (MW=1100, 66.5g, see formula 3.1) into a 500mL four-neck flask equipped with mechanical stirring, temperature controller, and dripping device, and add deionized water (33.5g) at the same time, Heat up while stirring and dissolving; prepare the solution of monomer B and monomer C, that is, the solution of acrylic acid (17.4g, see formula 3.2) and 1-phenylacrylic acid (4.64g, see formula 3.3); prepare reducing agent and The solution of chain transfer agent, is about to ascorbic acid (0.08g), thioglycolic acid (0.21g) are dissolved in deionized water (52g); Preparation oxidizing agent solution, mass concentration is that 30% hydrogen peroxide (0.22g) is dissolved in deionized water (7.5g); when the temperature in the reaction bottle is 60~65°C, first add the oxidizing agent solution, after stirring for 5 minutes, then dropwise add the solution of monomer B and monomer C and the solution of reducing agent and chain transfer agent at th...
PUM
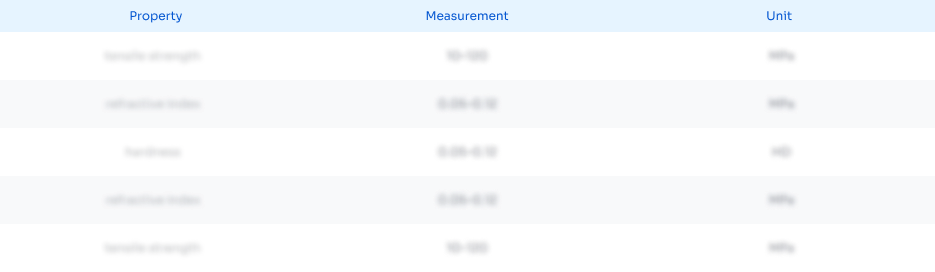
Abstract
Description
Claims
Application Information

- R&D
- Intellectual Property
- Life Sciences
- Materials
- Tech Scout
- Unparalleled Data Quality
- Higher Quality Content
- 60% Fewer Hallucinations
Browse by: Latest US Patents, China's latest patents, Technical Efficacy Thesaurus, Application Domain, Technology Topic, Popular Technical Reports.
© 2025 PatSnap. All rights reserved.Legal|Privacy policy|Modern Slavery Act Transparency Statement|Sitemap|About US| Contact US: help@patsnap.com