A kind of loose fiber dyeing device
A dyeing device and loose fiber technology, applied in liquid/gas/steam fiber/sliver/roving processing, textiles and papermaking, textile processing machine accessories, etc., can solve the problem of loose fiber loosening, uneven distribution of loose fiber, Prolong processing time and other issues to achieve the effect of avoiding insufficient fiber opening, strengthening uniform distribution, and stable transportation
- Summary
- Abstract
- Description
- Claims
- Application Information
AI Technical Summary
Problems solved by technology
Method used
Image
Examples
Embodiment 1
[0032] The loose fiber dyeing device of this embodiment combines figure 1 , including cotton grabbing device 1, web forming device 2, liquid soaking device 3, liquid squeezing device 4, coil forming device 5, cold stack color fixing device 6, uncoiling device 7, water washing device 8, water squeezing device 9 installed in sequence , fiber opening device 10 and drying device 12, a feeding belt (feeding belt one 100) is set between the water rolling device 9 and the fiber opening device 10, and the loose fiber web after water rolling is sent to the fiber opening device place for fiber opening, The loose fibers after fiber treatment are sent to the drying device 12 for drying under the drive of the feeding belt (feeding belt one 100). Above the feeding belt (feeding belt one 100), it is used to open the loose fiber web.
[0033] The loose fibers to be processed are picked up by the grabbing device 1 and sent to the web forming device 2, where the fiber web is formed in the web ...
Embodiment 2
[0038] The loose fiber dyeing device of this embodiment combines figure 2 , including cotton grabbing device 1, web forming device 2, liquid soaking device 3, liquid squeezing device 4, coil forming device 5, cold stack color fixing device 6, uncoiling device 7, water washing device 8, water squeezing device 9 installed in sequence , fiber opening device 10 and drying device 12, a feeding belt 100 is set between the water rolling device 9 and the fiber opening device 10, and the loose fiber web after water rolling is sent to the fiber opening device place for fiber opening, and the fiber opening process includes opening The fiber roll 101 and the fine fiber opening parts arranged behind the fiber opening roll 101, the fiber opening roll 101 is located above the feeding belt one 100, and is used for pre-opening the loose fiber web; the fiber opening roll 101 and the fine fiber opening parts A feeding belt 2 102 for conveying pre-opened loose fibers is arranged between them. Th...
Embodiment 3
[0044] The loose fiber dyeing device of this embodiment combines image 3 , including cotton grabbing device 1, web forming device 2, liquid soaking device 3, liquid squeezing device 4, coil forming device 5, cold stack color fixing device 6, uncoiling device 7, water washing device 8, water squeezing device 9 installed in sequence , fiber opening device 10, fiber laying device 11 and drying device 12, feeding belt 100 is set between water rolling device 9 and fiber opening device 10, fiber laying device 11 is arranged between fiber opening device 10 and drying device 12 , The web laying device 11 comprises a lower guide belt 110, an upper guide belt 112, a lower pressure roller 113, an upper pressure roller 114, a pair of lower driving rollers 110 and a pair of upper driving rollers 115, and the lower guiding belt 110 is set between the lower driving rollers 110 In between, the upper guide belt 112 is set between the upper drive rollers 115, the upper pressure roller 114 and ...
PUM
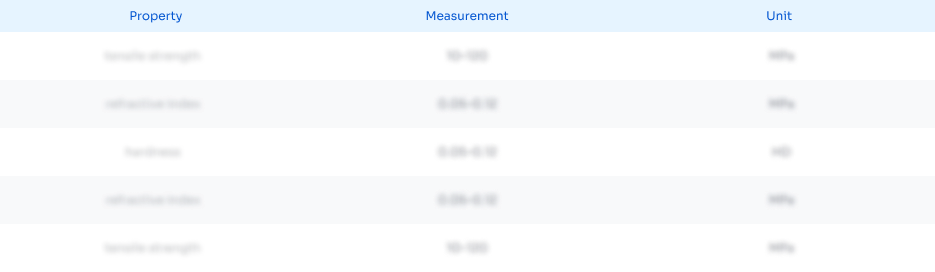
Abstract
Description
Claims
Application Information

- Generate Ideas
- Intellectual Property
- Life Sciences
- Materials
- Tech Scout
- Unparalleled Data Quality
- Higher Quality Content
- 60% Fewer Hallucinations
Browse by: Latest US Patents, China's latest patents, Technical Efficacy Thesaurus, Application Domain, Technology Topic, Popular Technical Reports.
© 2025 PatSnap. All rights reserved.Legal|Privacy policy|Modern Slavery Act Transparency Statement|Sitemap|About US| Contact US: help@patsnap.com