Wax-based blade coating patterning method
A patterned and patterned technology, applied in the field of micromachining, to achieve the effect of less sample injection, high stability and easy preparation
- Summary
- Abstract
- Description
- Claims
- Application Information
AI Technical Summary
Problems solved by technology
Method used
Image
Examples
Embodiment 1
[0033] Example 1 The patterning method based on scraping on wax is used for photonic crystal patterning:
[0034] (1) Hydrophilic treatment of polypropylene plastic sheet (PP), using 1%-10% (w / w) Tween-20 aqueous solution, soaking in piranha solution or Plasma plasma treatment machine, etc.
[0035] (2) Use CorelDraw12 to design the pattern SEU (length 1.5 mm, width 0.6 mm), and use a wax jet printer to print the wax pattern on PP.
[0036] (3) Five different particle sizes (200, 240, 270, 288, 950 nm) of SiO 2 Photonic crystal colloid aqueous solution (mass fraction 40%) is applied on the printed PP with a scraper.
[0037] (4) The solvent evaporates naturally at room temperature, and SiO 2 The nanoparticles form photonic crystal patterns in the wax-free hollow areas. And have the characteristics of color change when viewed from different angles ( image 3 )
[0038] (5) Reflection spectrum characterization of the pattern ( Figure 4 ) and SEM characterization ( Figur...
Embodiment 2
[0039] Example 2 The patterning method based on scraping coating on wax is used to pattern cellulose to make a microfluidic chip:
[0040] (1) Hydrophilic treatment of PP surface with 1% (w / w) Tween-20 aqueous solution
[0041] (2) Use CorelDraw12 to design microfluidic patterns (the narrowest channel width is 50 μm), and use a wax jet printer to print the wax patterns on PP.
[0042] (3) Microcrystalline cellulose with small particle size was prepared by acidolysis of microcrystalline cellulose: 10 g of microcrystalline cellulose (particle size ~20 μm) was added to 10 mL of sulfuric acid (mass fraction 64%), mixed thoroughly Stir at high speed at 45 ℃ for 30 min, centrifuge and wash several times to make the suspension pH = 7, then use an ultrasonic cell disruptor (S-450D) to ultrasonically break it for 10 min (50W), then ultrasonically disperse for 30 min, and freeze-dry to obtain For microcrystalline cellulose with a particle size of about 1-10 μm, a certain mass of acid-h...
PUM
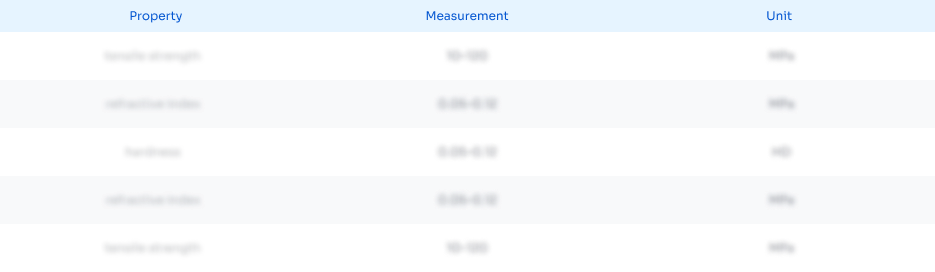
Abstract
Description
Claims
Application Information

- R&D
- Intellectual Property
- Life Sciences
- Materials
- Tech Scout
- Unparalleled Data Quality
- Higher Quality Content
- 60% Fewer Hallucinations
Browse by: Latest US Patents, China's latest patents, Technical Efficacy Thesaurus, Application Domain, Technology Topic, Popular Technical Reports.
© 2025 PatSnap. All rights reserved.Legal|Privacy policy|Modern Slavery Act Transparency Statement|Sitemap|About US| Contact US: help@patsnap.com