Swing rod and sliding block reciprocating type solar wing auxiliary turnover mechanism
A reversing mechanism and reciprocating technology, which is applied in space navigation equipment, simulation devices of space navigation conditions, transportation and packaging, etc., can solve the problem that the solar wing cannot be freely unfolded and folded, and achieve good scalability and simple structure Effect
- Summary
- Abstract
- Description
- Claims
- Application Information
AI Technical Summary
Problems solved by technology
Method used
Image
Examples
specific Embodiment approach 1
[0013] Specific implementation mode one: combine Figure 1-Figure 8 Describe this embodiment. In this embodiment, the pendulum slider reciprocating solar wing auxiliary turning mechanism includes a power device, a support mechanism, a transition shaft, a transmission device and two rocker mechanisms. The transition shaft is rotatably arranged on the support mechanism. The transmission device is set in the middle of the transition shaft, the power device is connected with the transmission device, and the two ends of the transition shaft are respectively rotatable and equipped with a rocker mechanism.
[0014] The power device includes a base 1, a rack 2, a lead screw 3 and a motor servo system 4, the rack 2 is slidably laid on the base 1, the motor servo system 4 is fixedly arranged on the base 1, and the lead screw 3 is arranged on the base 1 and connected to the output end of the motor servo system 4, the lead screw 3 is meshed with the rack 2;
[0015] The transition shaft ...
specific Embodiment approach 2
[0018] Specific implementation mode two: combination figure 1 Describe this embodiment, the supporting mechanism of this embodiment comprises two supports 18, two base plates 30 and a plurality of sliding bearings 19, the lower ends of two supports 18 are respectively fixedly arranged on the ground through a base plate 30, the two supports 18 The upper ends are respectively provided with a plurality of sliding bearings 19 . With such arrangement, the structure is simple, the stability is high, and it is convenient to support the power device, the transition shaft, the transmission device and the two rocker arm mechanisms. Other compositions and connections are the same as in the first embodiment.
specific Embodiment approach 3
[0019] Specific implementation mode three: combination figure 1 with Figure 5 Referring to this embodiment, the transmission device of this embodiment further includes two pins 20 , and the two ends of the gear shaft 10 are respectively connected to the left coupling 5 and the right coupling 6 through one pin 20 . With such a setting, the connection method is simple, and it is convenient for installation and maintenance. Other compositions and connections are the same as those in the second embodiment.
PUM
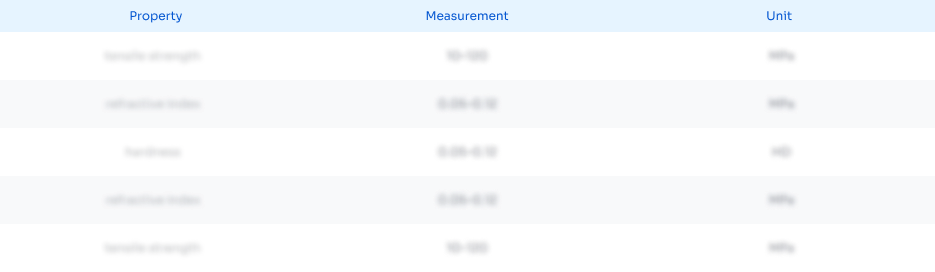
Abstract
Description
Claims
Application Information

- R&D
- Intellectual Property
- Life Sciences
- Materials
- Tech Scout
- Unparalleled Data Quality
- Higher Quality Content
- 60% Fewer Hallucinations
Browse by: Latest US Patents, China's latest patents, Technical Efficacy Thesaurus, Application Domain, Technology Topic, Popular Technical Reports.
© 2025 PatSnap. All rights reserved.Legal|Privacy policy|Modern Slavery Act Transparency Statement|Sitemap|About US| Contact US: help@patsnap.com