Raw material crushing system with back blowing function
A raw material crushing and functional technology, applied in grain processing and other directions, can solve the problems of material deposition, uneven particles, and easy deposition of materials, and achieve the effect of avoiding raw material deposition and uniform particles
- Summary
- Abstract
- Description
- Claims
- Application Information
AI Technical Summary
Problems solved by technology
Method used
Image
Examples
Embodiment 1
[0017] Such as figure 1 , figure 2 As shown, a raw material crushing system with a back blowing function is provided, including a hollow support box 1, a crushing chamber and a motor 4 are arranged on the top surface of the support box 1, and the crushing chamber and the motor 4 are fixed on the support box 1, a hopper 6 is installed on the crushing chamber, and the hopper 6 communicates with the interior of the crushing chamber. A cylindrical cavity is provided inside the crushing chamber, and the motor 4 is connected to a rotating shaft 14, and the rotating shaft 14 is far away from the motor. One end of 4 extends into the cavity, and the rotating shaft 14 is sleeved with a chopping runner 15, and the chopping runner 15 is arranged inside the cavity, and a pipeline 20 is arranged on the side wall of the support box 1, and one end of the pipeline 20 An air pump 21 is connected, and the air pump 21 is arranged on the outside of the support box 1. The other end of the pipelin...
Embodiment 2
[0019] Such as figure 1 , figure 2As shown, on the basis of Embodiment 1, the crushing chamber includes a housing 5 with an opening at one end, an end cover 3 is arranged on the housing 5, and the end cover 3 seals the opening end of the housing 5, and the end cover 3 and the motor 4 are respectively arranged on the symmetrical sides of the casing 5, the cavity is arranged in the casing 5, the dust screen 19 is arranged on the casing 5, the casing 5 is installed on the supporting box 1, and the casing 5 is set There are two fixed buckles, one end of the fixed buckle is fixed with the housing 5, a rotating pin is arranged between the fixed buckles, the two ends of the rotating pin pass through the two fixing buckles respectively, the end cover 3 is connected with the rotating pin, and the end cover 3 It can rotate around the rotating pin; the housing 5 is provided with two mutually parallel mounting blocks 11, one end of the mounting blocks 11 is fixed to the outer wall of th...
PUM
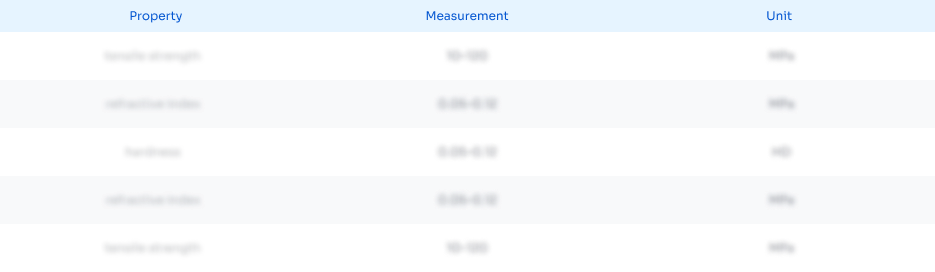
Abstract
Description
Claims
Application Information

- R&D
- Intellectual Property
- Life Sciences
- Materials
- Tech Scout
- Unparalleled Data Quality
- Higher Quality Content
- 60% Fewer Hallucinations
Browse by: Latest US Patents, China's latest patents, Technical Efficacy Thesaurus, Application Domain, Technology Topic, Popular Technical Reports.
© 2025 PatSnap. All rights reserved.Legal|Privacy policy|Modern Slavery Act Transparency Statement|Sitemap|About US| Contact US: help@patsnap.com