Resid catalytic cracker and catalyst for increased propylene yield
A cracking catalyst and catalyst technology, applied in the direction of catalytic cracking, physical/chemical process catalyst, metal/metal oxide/metal hydroxide catalyst, etc., can solve the problem of reducing the negative impact of catalyst activity and selectivity
- Summary
- Abstract
- Description
- Claims
- Application Information
AI Technical Summary
Problems solved by technology
Method used
Image
Examples
Embodiment Construction
[0014] In the method for increasing the yield of propylene, the light naphtha feedstock is obtained from the residual oil catalytic cracking zone. Any catalytic cracking process or apparatus may be used as the primary cracking zone, including those suitable for processing catalytic cracking feedstocks derived from atmospheric or vacuum residues. An example of this method includes figure 1 Residual Catalytic Cracking Process ("RFCC") licensed from UOP, LLC as indicated.
[0015] In some typical embodiments, the catalytic cracking zone uses a fluidized bed process. The cracking catalyst is combined with the lift gas and the catalytic cracker feed at the inlet of the first riser reactor 10 . The catalytic cracker feedstock is resid with vanadium, sodium or a combination thereof. It is also contemplated that the feedstock contains other metals, including but not limited to nickel and zinc. Vanadium is present in an amount of 20-400 ppm, preferably 20-150 ppm, more preferably a...
PUM
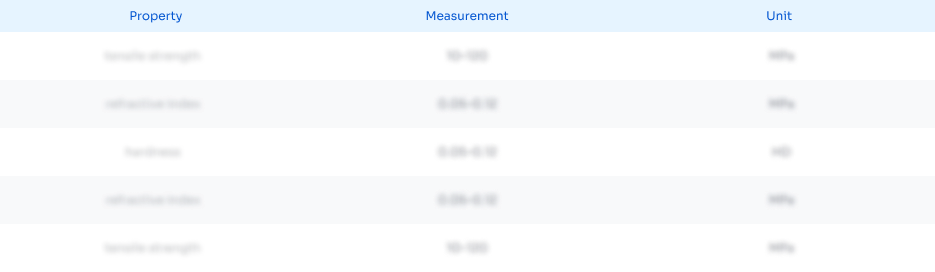
Abstract
Description
Claims
Application Information

- R&D Engineer
- R&D Manager
- IP Professional
- Industry Leading Data Capabilities
- Powerful AI technology
- Patent DNA Extraction
Browse by: Latest US Patents, China's latest patents, Technical Efficacy Thesaurus, Application Domain, Technology Topic, Popular Technical Reports.
© 2024 PatSnap. All rights reserved.Legal|Privacy policy|Modern Slavery Act Transparency Statement|Sitemap|About US| Contact US: help@patsnap.com