Preparation method of viscosity-reduction type polycarboxylate water reducer
A technology of viscous polycarboxylic acid and water reducer, which is applied in the field of concrete admixtures in building materials, can solve the problems of high viscosity, achieve high dispersion, obvious viscosity reduction effect, and good adaptability
- Summary
- Abstract
- Description
- Claims
- Application Information
AI Technical Summary
Problems solved by technology
Method used
Image
Examples
Embodiment 1
[0026] 1) Put 100 parts of methyl alkenyl polyoxyethylene ether (see general formula 1 for molecular structure, n=50) into the bottom of the kettle, add 100 parts of deionized water, heat up to 60°C, stir to dissolve, and then put 10 parts of butyl acrylate Parts, 70 parts of random polyoxyethylene oxypropylene ether acrylate (see general formula 1 for molecular structure, m=50, q=10, z=0), stir evenly;
[0027] 2) Control the temperature at 60°C, add 3.5 parts of potassium persulfate into the kettle, and stir for 10 minutes;
[0028] 3) Control the temperature at 60°C, add dropwise a mixed solution containing 15 parts of acrylic acid, 1.2 parts of mercaptoethanol and 15 parts of deionized water for 3 hours;
[0029] 4) Continue to keep warm for 2 hours
[0030] 5) Cool down to 35°C-40°C, add 30% liquid caustic soda to neutralize, and adjust the pH value to 5. Add water and dilute to 40% concentration to obtain the product VPC-1 of the present invention.
Embodiment 2
[0032] 1) Put 100 parts of methyl alkenyl polyoxyethylene ether (see general formula 1 for molecular structure, n=50) into the bottom of the kettle, add 100 parts of deionized water, heat up to 60°C, stir to dissolve, and then put in butyl acrylate 5 70 parts, 70 parts of methoxy atactic polyoxyethylene oxypropylene ether acrylate (see general formula 1 for molecular structure, m=50, q=20, z=0), stir evenly;
[0033] 2) Control the temperature at 60°C, add 3.5 parts of potassium persulfate into the kettle, and stir for 10 minutes;
[0034] 3) Control the temperature at 60°C, add dropwise a mixed solution containing 15 parts of acrylic acid, 1.2 parts of mercaptoethanol and 15 parts of deionized water for 3 hours;
[0035] 4) Continue to keep warm for 2 hours
[0036] 5) Cool down to 35°C-40°C, add 30% liquid caustic soda to neutralize, and adjust the pH value to 5. Add water and dilute to 40% concentration to obtain the product VPC-2 of the present invention.
Embodiment 3
[0038] 1) Put 100 parts of methyl alkenyl polyoxyethylene ether (see general formula 1 for molecular structure, n=50) into the bottom of the kettle, add 100 parts of deionized water, heat up to 60°C, stir to dissolve, and then put in butyl acrylate 5 70 parts, 70 parts of methoxy atactic polyoxyethylene oxypropylene oxybutylene acrylate (see general formula 1 for molecular structure, m=50, q=20, z=20), stir evenly;
[0039] 2) Control the temperature at 60°C, add 3.5 parts of potassium persulfate into the kettle, and stir for 10 minutes;
[0040] 3) Control the temperature at 60°C, add dropwise a mixed solution containing 15 parts of acrylic acid, 1.2 parts of mercaptoethanol and 15 parts of deionized water for 3 hours;
[0041] 4) Continue to keep warm for 2 hours
[0042] 5) Cool down to 35°C-40°C, add 30% liquid caustic soda to neutralize, and adjust the pH value to 5. Add water and dilute to 40% concentration to obtain the product VPC-3 of the present invention.
PUM
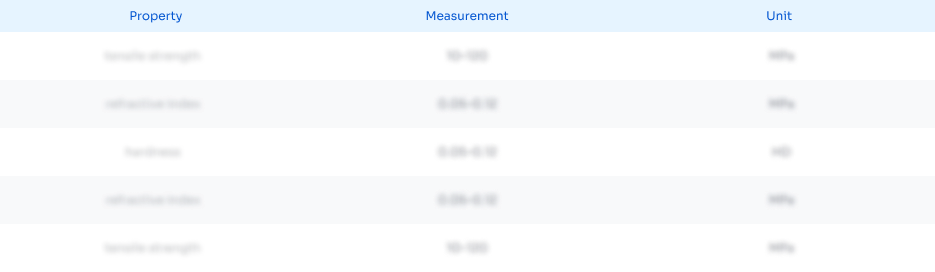
Abstract
Description
Claims
Application Information

- R&D Engineer
- R&D Manager
- IP Professional
- Industry Leading Data Capabilities
- Powerful AI technology
- Patent DNA Extraction
Browse by: Latest US Patents, China's latest patents, Technical Efficacy Thesaurus, Application Domain, Technology Topic, Popular Technical Reports.
© 2024 PatSnap. All rights reserved.Legal|Privacy policy|Modern Slavery Act Transparency Statement|Sitemap|About US| Contact US: help@patsnap.com