Method for preparing cyanobenzene by ammonifying benzoic acid gaseous phase
A technology of benzoic acid and benzonitrile, which is applied in the fields of ammonia-carboxylic acid reaction preparation, organic chemistry, etc., can solve the problems of high requirements for condition control, complicated three-waste treatment technology, and complicated technological process.
- Summary
- Abstract
- Description
- Claims
- Application Information
AI Technical Summary
Problems solved by technology
Method used
Image
Examples
Embodiment 1
[0018] The catalyst was filled in a tubular fixed-bed reactor, and hydrogen was continuously fed into the fixed-bed reactor at 300° C. to activate the catalyst for 2 hours. Nitrogen is used as the carrier gas to pass into the preheater. When nitrogen flows through the vaporization chamber, it is mixed with vaporized benzoic acid and ammonia to form a mixed gas of benzoic acid-ammonia-nitrogen. The molar ratio of each substance in the mixed gas is benzoic acid : ammonia: nitrogen = 1:1:5; benzoic acid-ammonia-nitrogen mixed gas reacts at 400°C when it passes through the catalyst bed, and the crude product obtained by the reaction is liquefied in the condenser, and the cooling medium in the condenser is water , The crude product can be rectified after separating the water phase, and the benzonitrile content in the crude product is 85wt%. The unliquefied gas can be back-pressurized by the compressor to the gas tank for recycling. The present invention prepares the technological ...
Embodiment 2
[0021] The catalyst is filled in a tubular fixed-bed reactor, and hydrogen is continuously fed into the fixed-bed reactor at 320°C to activate the catalyst for 2 hours; hydrogen and nitrogen are mixed and passed into the preheater as a carrier gas, in which hydrogen and nitrogen The molar ratio of the hydrogen-nitrogen mixture is 1:1; when the hydrogen-nitrogen mixed gas flows through the vaporization chamber, it is mixed with the vaporized benzoic acid and urea to form a mixed gas of benzoic acid-urea-hydrogen-nitrogen, and the molar ratio of each substance in the mixed gas is benzene Formic acid: urea: hydrogen: nitrogen = 1:2:20:20; when the mixed gas of benzoic acid-urea-hydrogen-nitrogen passes through the catalyst bed, the reaction occurs at 350°C, and the crude product obtained by the reaction is liquefied in the condenser and then The cooling medium is glycerin, and the crude product can be rectified after separating the water phase. The benzonitrile content in the cru...
Embodiment 3
[0024] Fill phosphoric acid-diatomaceous earth in a tubular fixed reactor as a catalyst, and continuously pass hydrogen gas into the fixed-bed reactor at 250°C to activate phosphoric acid-diatomite for 2 hours; use water vapor as carrier gas to preheat When water vapor flows through the vaporization chamber, it is mixed with vaporized benzoic acid and ammonium bicarbonate to form a mixed gas of benzoic acid-ammonia-steam, and the molar ratio of each substance in the mixed gas is benzoic acid: ammonium bicarbonate: water Steam=1:5:30; benzoic acid-ammonia-steam mixed gas reacts at 250°C when it passes through the catalyst bed, and the crude product obtained from the reaction is liquefied in the condenser, and the cooling medium in the condenser is heat transfer oil , The crude product can be rectified after separating the water phase, and the content of benzonitrile in the crude product is 80 wt%. Unliquefied gas can be vented.
[0025]
[0026] The ammoniating agent ammonia,...
PUM
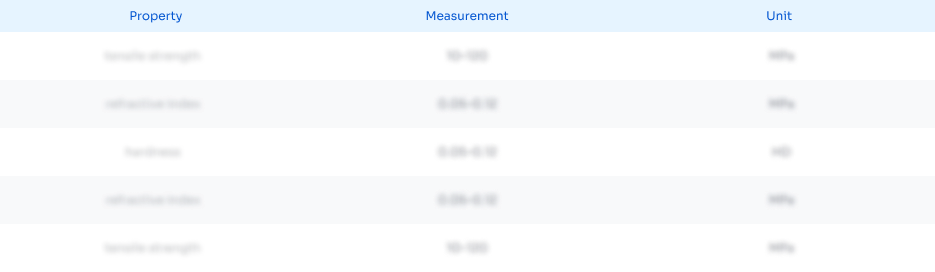
Abstract
Description
Claims
Application Information

- Generate Ideas
- Intellectual Property
- Life Sciences
- Materials
- Tech Scout
- Unparalleled Data Quality
- Higher Quality Content
- 60% Fewer Hallucinations
Browse by: Latest US Patents, China's latest patents, Technical Efficacy Thesaurus, Application Domain, Technology Topic, Popular Technical Reports.
© 2025 PatSnap. All rights reserved.Legal|Privacy policy|Modern Slavery Act Transparency Statement|Sitemap|About US| Contact US: help@patsnap.com