Heat treatment deformation control method of thin-wall saddle-shaped aluminum alloy casting
An aluminum alloy casting and heat treatment deformation technology, which is used in the heat treatment deformation control of cast aluminum alloy, the heat treatment deformation control of thin-walled saddle-shaped aluminum alloy castings, and the heat treatment of large thin-walled cast aluminum alloy parts. Complex structure, affecting product processing and final use, etc., to achieve the effect of easy operation, high performance, and avoiding difficult control of precision
- Summary
- Abstract
- Description
- Claims
- Application Information
AI Technical Summary
Problems solved by technology
Method used
Image
Examples
Embodiment 1
[0032] The first step is to install the tooling: install the blocking tooling at both ends of the casting, and the structure of the blocking plate is as follows image 3 . Three clamps are installed at the front, rear and middle of the open part, and the positions of the three clamps are specified. The front clamp 6 is 60mm from the front, the middle clamp 8 is 600mm from the front, and the rear clamp 7 is from the front. 1200mm position. And apply pre-tightening force to the adjustable bolts, the front clamp 6 requires the adjustable bolts to be tight inside and loose outside, the rear clamp 7 requires the adjustable bolts to be tight outside and loose inside, and the internal and external constraints of the middle clamp 8 are consistent.
[0033] The second step is to determine the way of entering the furnace: choose the rear end 2 to face down, and place the castings vertically. Solid solution adopts bottom-pumping aluminum alloy quenching furnace. The method of entering...
Embodiment 2
[0040] The first step is to install the tooling: install the blocking tooling at both ends of the casting, and the structure of the blocking plate is as follows image 3 . Three clamps are installed on the open part, and the positions of the three clamps are specified. The front clamp 6 is 60mm from the front end, the middle clamp 8 is 600mm from the front end, and the rear clamp 7 is 1200mm from the front face. And apply pre-tightening force to the adjustable bolts, the front clamp 6 requires the adjustable bolts to be tight inside and loose outside, the rear clamp 7 requires the adjustable bolts to be tight outside and loose inside, and the internal and external constraints of the middle clamp 8 are consistent.
[0041] The second step is to determine the way of entering the furnace: select the rear end 2 to face down, and place the castings vertically. Solid solution adopts bottom-pumping aluminum alloy quenching furnace. The method of entering the furnace is as Figure ...
Embodiment 3
[0047] Embodiment 3: be the best embodiment of the present invention
[0048] The first step is to install the tooling: install the blocking tooling at both ends of the casting, and the structure of the blocking plate is as follows image 3 . Three clamps are installed on the open part, and the positions of the three clamps are specified. The front clamp 6 is 60mm from the front, the middle clamp 8 is 600mm from the front, and the rear clamp 7 is 1200mm from the front. And apply pretightening force to the adjustable bolts, the front clamp 6 requires the adjustable bolts to be tight inside and loose outside, the rear clamp 7 requires the adjustable bolts to be tight outside and loose inside, and the internal and external constraints of the middle clamp 8 are consistent.
[0049] The second step is to determine the way of entering the furnace: choose the rear end 2 to face down, and place the castings vertically. Solid solution adopts bottom-pumping aluminum alloy quenching fu...
PUM
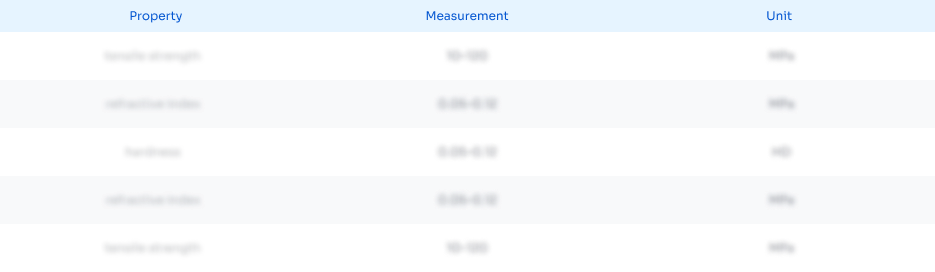
Abstract
Description
Claims
Application Information

- R&D
- Intellectual Property
- Life Sciences
- Materials
- Tech Scout
- Unparalleled Data Quality
- Higher Quality Content
- 60% Fewer Hallucinations
Browse by: Latest US Patents, China's latest patents, Technical Efficacy Thesaurus, Application Domain, Technology Topic, Popular Technical Reports.
© 2025 PatSnap. All rights reserved.Legal|Privacy policy|Modern Slavery Act Transparency Statement|Sitemap|About US| Contact US: help@patsnap.com