Poplar sheet material surface layer reinforcement method
A board and surface technology, applied in the field of poplar board surface strengthening, can solve problems such as waste and uncontrollable compression, and achieve the effects of saving resources, high dimensional stability, and high yield.
- Summary
- Abstract
- Description
- Claims
- Application Information
AI Technical Summary
Problems solved by technology
Method used
Image
Examples
Embodiment 1
[0029] A method for strengthening the surface of a poplar board, specifically comprising the following steps: (1) board preparation; (2) planing the surface; (3) softening the surface; (4) compressing the surface; (5) stabilizing treatment. Firstly, the poplar logs are sawed into boards of a certain thickness according to the needs, and the surface layer is softened after planing. The softened boards are quickly loaded into a press for surface compression. The compression-molded boards are ready after stabilization. Can.
[0030] In above-mentioned steps, softening treatment step is:
[0031] (1a) Saw poplar plank, thickness 30mm, select the plank (preferably string-cut wood) and dry to 15% moisture content, double-sided planing with fixed thickness, planed board thickness is 22mm (finished board thickness 18mm). Then cut the length and width of the plate according to the width of the hot press, and remove defects (knots, insect eyes, decay, etc.) at the same time.
[0032] ...
Embodiment 2
[0043] A method for strengthening the surface of a poplar board, specifically comprising the following steps: (1) board preparation; (2) planing the surface; (3) softening the surface; (4) compressing the surface; (5) stabilizing treatment. Firstly, the poplar logs are sawed into boards of a certain thickness according to the needs, and the surface layer is softened after planing. The softened boards are quickly loaded into a press for surface compression. The compression-molded boards are ready after stabilization. Can.
[0044] In above-mentioned steps, softening treatment step is:
[0045] (1a) Saw poplar boards with a thickness of 25mm, select the boards and dry them to a moisture content of 20%, and plan on both sides with a fixed thickness. The thickness of the planed boards is 19mm (the thickness of the finished board is 15mm). Then cut the length and width of the plate according to the width of the hot press, and remove defects (knots, insect eyes, decay, etc.) at the...
PUM
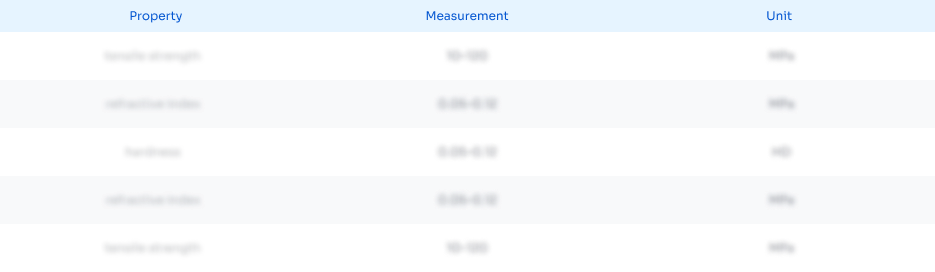
Abstract
Description
Claims
Application Information

- R&D
- Intellectual Property
- Life Sciences
- Materials
- Tech Scout
- Unparalleled Data Quality
- Higher Quality Content
- 60% Fewer Hallucinations
Browse by: Latest US Patents, China's latest patents, Technical Efficacy Thesaurus, Application Domain, Technology Topic, Popular Technical Reports.
© 2025 PatSnap. All rights reserved.Legal|Privacy policy|Modern Slavery Act Transparency Statement|Sitemap|About US| Contact US: help@patsnap.com