Manufacturing method for multilayer thick copper circuit board and manufacturing method for two-sided thick copper circuit board
A production method and thick copper plate technology, which is applied in multilayer circuit manufacturing, printed circuit manufacturing, printed circuit, etc., can solve the problems of insufficient, explosive boards, and the inability to make fine line glue filling, etc., and achieve the effect of increasing line density
- Summary
- Abstract
- Description
- Claims
- Application Information
AI Technical Summary
Problems solved by technology
Method used
Image
Examples
Embodiment Construction
[0026] In order to solve the technical problems in the prior art that fine lines cannot be produced during the etching process of thick copper circuit boards and holes are formed due to insufficient glue filling in the pressing process, resulting in easy board explosion, the general idea is as follows:
[0027] In the embodiment of the present invention, the etching and lamination of the thick copper circuit board are processed step by step. First, the two layers of copper boards are pressed together by means of a peelable adhesive sheet. This peelable adhesive sheet can firmly bond the copper boards at room temperature. Together, but after the high temperature in the subsequent pressing process, this peelable adhesive sheet made of polymer materials will crack and lose its bonding effect, so the two copper plates can be separated again.
[0028] When etching, because of the existence of the peelable adhesive sheet, it is possible to etch two copper plates at the same time in o...
PUM
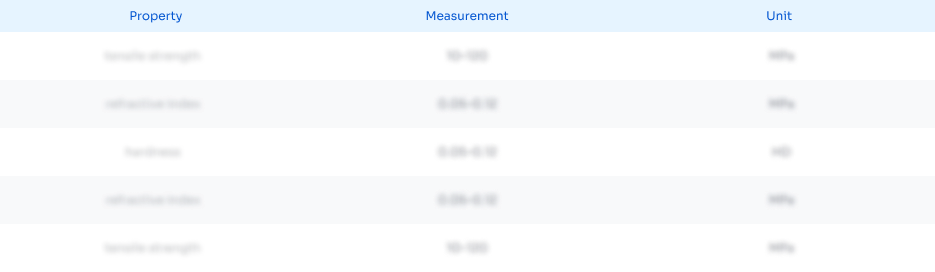
Abstract
Description
Claims
Application Information

- Generate Ideas
- Intellectual Property
- Life Sciences
- Materials
- Tech Scout
- Unparalleled Data Quality
- Higher Quality Content
- 60% Fewer Hallucinations
Browse by: Latest US Patents, China's latest patents, Technical Efficacy Thesaurus, Application Domain, Technology Topic, Popular Technical Reports.
© 2025 PatSnap. All rights reserved.Legal|Privacy policy|Modern Slavery Act Transparency Statement|Sitemap|About US| Contact US: help@patsnap.com