Method for preparing flame-retardant fabric finishing agent
A flame-retardant finishing agent and fabric technology, which is applied in fiber treatment, textiles and papermaking, etc., can solve problems such as not being resistant to washing and dry cleaning, fabric flame resistance and late-flammability not meeting requirements, and unsatisfactory effects, etc. Achieve good flame resistance and latent ignition, and prevent dripping effects
- Summary
- Abstract
- Description
- Claims
- Application Information
AI Technical Summary
Problems solved by technology
Method used
Examples
Embodiment 1
[0012] A preparation method of a fabric flame retardant finishing agent, comprising the steps of:
[0013] 1) Take 3 parts by mass of diammonium hydrogen phosphate, 17 parts by mass of borax, 9 parts by mass of trimethyloltripolyamide, 3 parts by mass of tetrahydroxyethylphosphorus chloride, and 7 parts by mass of sodium silicate, and mix them uniformly;
[0014] 2) Then add 3 parts by mass of dodecyltrimethylammonium sulfate, 6 parts by mass of magnesium chloride, 180 parts by mass of deionized water, and 15 parts by mass of tricresyl phosphate. The feeding is completed within 20 minutes, and the mixture is evenly mixed at 65°C ;
[0015] 3) Cool to room temperature, add 3 parts by mass of hydroxypropyl methylcellulose, 14 parts by mass of triethanolamine, and 9 parts by mass of urea in sequence, and stir and mix evenly to obtain a fabric flame-retardant finishing agent.
Embodiment 2
[0017] A preparation method of a fabric flame retardant finishing agent, comprising the steps of:
[0018] 1) Take 2 parts by mass of diammonium hydrogen phosphate, 15 parts by mass of borax, 8 parts by mass of trimethyloltripolyamide, 2 parts by mass of tetrahydroxyethylphosphorus chloride, and 6 parts by mass of sodium silicate, and mix them uniformly;
[0019] 2) Then add 2 parts by mass of dodecyltrimethylammonium sulfate, 5 parts by mass of magnesium chloride, 150 parts by mass of deionized water, and 10 parts by mass of tricresyl phosphate. The feeding is completed within 15 minutes, and the mixture is evenly mixed at 60°C ;
[0020] 3) Cool to room temperature, add 2 parts by mass of hydroxypropyl methylcellulose, 12 parts by mass of triethanolamine, and 8 parts by mass of urea in sequence, and stir and mix evenly to obtain a fabric flame-retardant finishing agent.
Embodiment 3
[0022] A preparation method of a fabric flame retardant finishing agent, comprising the steps of:
[0023] 1) Take 2.3 parts by mass of diammonium hydrogen phosphate, 16 parts by mass of borax, 8.9 parts by mass of trimethyloltripolyamide, 2.3 parts by mass of tetrahydroxyethylphosphorus chloride, and 6.7 parts by mass of sodium silicate, and mix them uniformly;
[0024] 2) Then add 2.3 parts by mass of dodecyltrimethylammonium sulfate, 5.6 parts by mass of magnesium chloride, 170 parts by mass of deionized water, and 13 parts by mass of tricresyl phosphate, and complete the feeding within 17 minutes. Stir and mix evenly at 63°C ;
[0025] 3) Cool to room temperature, add 2.3 parts by mass of hydroxypropyl methylcellulose, 13 parts by mass of triethanolamine, and 8.9 parts by mass of urea in sequence, stir and mix evenly to obtain a fabric flame retardant finishing agent.
PUM
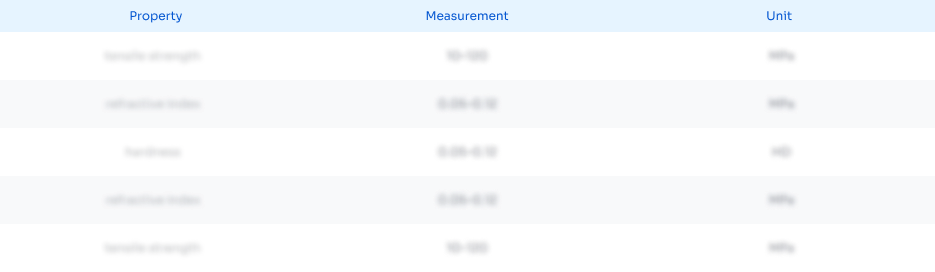
Abstract
Description
Claims
Application Information

- R&D
- Intellectual Property
- Life Sciences
- Materials
- Tech Scout
- Unparalleled Data Quality
- Higher Quality Content
- 60% Fewer Hallucinations
Browse by: Latest US Patents, China's latest patents, Technical Efficacy Thesaurus, Application Domain, Technology Topic, Popular Technical Reports.
© 2025 PatSnap. All rights reserved.Legal|Privacy policy|Modern Slavery Act Transparency Statement|Sitemap|About US| Contact US: help@patsnap.com