Method for preparing electrolyte-resistant printing paste with straw as raw material
A technology of electrolyte resistance and printing paste, which is applied in the fields of dyeing, textiles and papermaking, and can solve the problems of increased production cost of carboxymethyl cellulose, high production cost of carboxymethyl cellulose, and poor electrolyte resistance of paste , to achieve the effect of high degree of substitution, low production cost, and improved color fixation rate
- Summary
- Abstract
- Description
- Claims
- Application Information
AI Technical Summary
Problems solved by technology
Method used
Image
Examples
Embodiment 1
[0071] The straw was dedusted and crushed to 100 mesh. Add 800kg of ethylene glycol, 200kg of water, and 5kg of sulfuric acid into 2000L of the reaction kettle in sequence, mix well, add 200kg of micropowdered straw powder, cook at 120°C for 1.0 hour under stirring, cool down and filter, and wash the filter residue with hot water until neutral After drying, it is crude straw cellulose.
[0072] Adjust the stirring speed of 1000L agitator to 240r / min, slowly add 100kg of dried crude straw cellulose and 6kg of sodium tetraborate, continue stirring for 10min, and then add 100kg of methanol aqueous solution with a mass ratio of 80% by spraying. After continuing to stir for 12 minutes, slowly add 85kg of 200-mesh powdered sodium hydroxide, react at 25°C for 40min, then add 115kg of solid chloroacetic acid, and react at 75°C for 2h. After the reaction is finished, it is neutralized with acetic acid, the pH value is between 5-8, and the printing paste is obtained after drying and cr...
Embodiment 2
[0074] The straw is dedusted and crushed to 120 mesh. Add 900kg of ethylene glycol, 100kg of water, and 10kg of sulfuric acid into 2000L of the reaction kettle in sequence, mix well, add 200kg of micronized straw powder, cook at 130°C for 1.5 hours under stirring, cool down and filter, and wash the filter residue with hot water until neutral Drying is crude straw cellulose.
[0075] Adjust the stirring speed of the 1000L reactor to 320r / min, slowly add 100kg of dried straw cellulose and 7kg of sodium tetraborate, continue stirring for 12 minutes, then add 100kg of 85% ethanol aqueous solution by spraying, and continue stirring for 15 minutes Then slowly add 75kg of 200 mesh powder sodium hydroxide, react at 15°C for 1h, then add 105kg of solid chloroacetic acid, react at 70°C for 1.5h. After the reaction is finished, it is neutralized with acetic acid, the pH value is between 5-8, and the printing paste is obtained after drying and crushing.
PUM
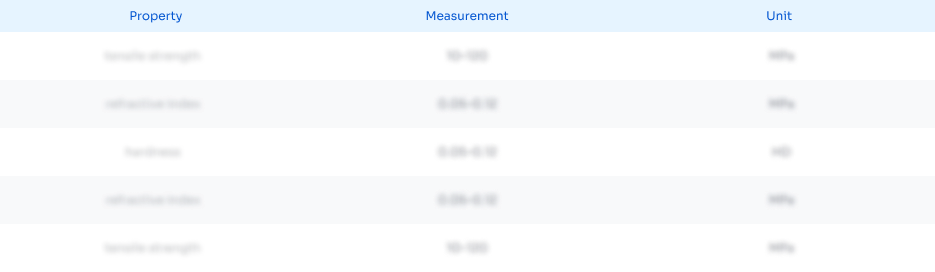
Abstract
Description
Claims
Application Information

- R&D
- Intellectual Property
- Life Sciences
- Materials
- Tech Scout
- Unparalleled Data Quality
- Higher Quality Content
- 60% Fewer Hallucinations
Browse by: Latest US Patents, China's latest patents, Technical Efficacy Thesaurus, Application Domain, Technology Topic, Popular Technical Reports.
© 2025 PatSnap. All rights reserved.Legal|Privacy policy|Modern Slavery Act Transparency Statement|Sitemap|About US| Contact US: help@patsnap.com