Preparation method of comb type high-molecular flotation agent
A comb-shaped polymer and flotation agent technology, applied in flotation, solid separation, etc., can solve the problems that one component is difficult to play multiple functions, cannot produce superimposed effects, and compatibility differences, etc., to achieve good emulsification effect, Simplify the pretreatment process and improve the effect of the interface state
- Summary
- Abstract
- Description
- Claims
- Application Information
AI Technical Summary
Problems solved by technology
Method used
Examples
Embodiment 1
[0023] Add 360g of allyl polyoxyethylene ether (m=12) into the glass kettle, and pass in nitrogen to replace the air in the kettle to maintain the nitrogen environment in the kettle. The temperature of the water bath was raised to 40°C to melt the material. Start stirring, and continuously add 45 g of phosphorus pentoxide along with nitrogen. Raise the temperature to 80°C and react for 4 hours to obtain allyl polyoxyethylene ether phosphate.
[0024] Add 200 g of the above-mentioned allyl polyoxyethylene ether phosphate, 22 g of octafluoropentyl alcohol polyoxyethylene ether acrylate (p=10), and 56 g of water into a glass kettle, fully dissolve and mix well. Mix 64g of acrylamide with 16g of water to make an 80% solution. Mix 1.75g of ammonium persulfate and 1.21g of thioglycolic acid to make an aqueous solution with a mass concentration of 10%. The water bath was warmed to 80°C. The acrylamide solution and the initiator solution were added dropwise, the acrylamide was a...
Embodiment 2
[0026] Add 300g of allyl polyoxyethylene ether (m=20) into the glass kettle, pass in nitrogen to replace the air in the kettle, and maintain the nitrogen environment in the kettle. The temperature of the water bath was raised to 40°C to melt the material. Start stirring, and continuously add 22 g of phosphorus pentoxide along with nitrogen. Raise the temperature to 80°C and react for 4 hours to obtain allyl polyoxyethylene ether phosphate.
[0027] Add 260g of the above-mentioned allyl polyoxyethylene ether phosphate, 37g of dodecafluoroheptyl alcohol polyoxyethylene ether methacrylate (p=12), and 95g of water into a glass kettle, fully dissolve and mix well. Mix 76g of acrylamide with 25g of water to make a 75% solution. Mix 2.22g of ammonium persulfate and 1.89g of thioglycolic acid to prepare an aqueous solution with a mass concentration of 20%. The temperature of the water bath was raised to 90°C. The acrylamide solution and the initiator solution were added dropwise, ...
Embodiment 3
[0029] Add 380g of allyl polyoxyethylene ether (m=18) into the glass kettle, and pass in nitrogen to replace the air in the kettle to maintain the nitrogen environment in the kettle. The temperature of the water bath was raised to 40°C to melt the material. Start stirring, and continuously add 32 g of phosphorus pentoxide along with nitrogen. Raise the temperature to 80°C and react for 4 hours to obtain allyl polyoxyethylene ether phosphate.
[0030] Add 200g of the above-mentioned allyl polyoxyethylene ether phosphate, 50g of perfluorooctyl alcohol polyoxyethylene ether acrylate (p=15), and 83g of water into a glass kettle, fully dissolve and mix well. Mix 70g of acrylamide with 18g of water to make an 80% solution. Mix 1.92g of ammonium persulfate and 2.07g of thioglycolic acid to prepare an aqueous solution with a mass concentration of 15%. The water bath was warmed to 85°C. The acrylamide solution and the initiator solution were added dropwise, the acrylamide was added...
PUM
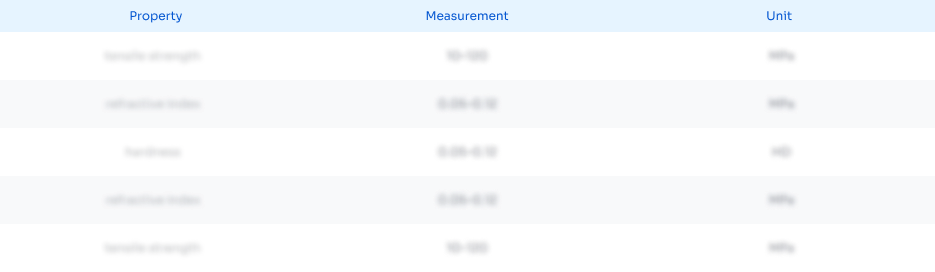
Abstract
Description
Claims
Application Information

- Generate Ideas
- Intellectual Property
- Life Sciences
- Materials
- Tech Scout
- Unparalleled Data Quality
- Higher Quality Content
- 60% Fewer Hallucinations
Browse by: Latest US Patents, China's latest patents, Technical Efficacy Thesaurus, Application Domain, Technology Topic, Popular Technical Reports.
© 2025 PatSnap. All rights reserved.Legal|Privacy policy|Modern Slavery Act Transparency Statement|Sitemap|About US| Contact US: help@patsnap.com