Method for preparing bis(2,4,4-trimethylpentyl) phosphinic acid from hydrogen phosphide as byproduct in sodium hypophosphite production process
A technology of trimethylpentyl and phosphinic acid, which is applied in chemical instruments and methods, organic chemistry, compounds of Group 5/15 elements of the periodic table, etc., and can solve problems such as pollution and waste
- Summary
- Abstract
- Description
- Claims
- Application Information
AI Technical Summary
Problems solved by technology
Method used
Examples
Embodiment 1
[0026] 7000 g of diisobutene (75% 2,4,4-trimethyl-1-pentene, 25% 2,4,4-trimethyl-2-pentene) was sucked into a stainless steel autoclave. The by-product crude phosphine (hereinafter referred to as crude phosphine) from the production of sodium hypophosphite is washed with 30% NaOH solution and then enters the freeze dryer, freeze-dried at 0-3°C to remove water, and then enters the high-pressure reaction pot through the compressor . The temperature in the pot is kept at -30~-20°C. When the pressure in the kettle rose to 50 atmospheres, the vent valve was opened to keep the 50 atmospheres in the kettle. The temperature of the solution in the high-pressure reaction kettle is maintained below -20°C. After maintaining this process for 1.5 hours, the input of crude phosphine gas was stopped. The pressure was released to 40 atmospheres, and 900 grams of phosphine was absorbed in the high-pressure reactor (total air flow rate of input was 2090 grams). When heating the high-p...
Embodiment 2
[0029] Dissolve 50 g of benzoyl peroxide in 7000 g of diisobutylene (75% 2,4,4-trimethyl-1-pentene, 25% 2,4,4-trimethyl-2-pentene). The resulting solution is sucked into a stainless steel high-pressure reaction kettle. Crude phosphine is washed with 50% NaOH solution, and then enters the freeze dryer, freeze-dried at 0-3°C to remove water, and then enters the high-pressure reaction pot through the compressor. The temperature in the kettle is maintained at -15°C~-20°C. When the pressure in the kettle rose to 60 atmospheres, the vent valve was opened to keep the 60 atmospheres in the kettle. This process was maintained for 2 hours, and the input of crude phosphine gas was stopped. The pressure in the high-pressure reaction kettle was released to 40 atmospheres, and 1361 grams of phosphine was absorbed in the high-pressure reaction kettle (the total air flow rate was 3404 grams). When the high-pressure reaction pot is heated to 80°C, the pressure inside the pot rises to 60-70 ...
Embodiment 3
[0032] Dissolve 136 g of benzoyl peroxide in 7000 g of diisobutylene (75% 2,4,4-trimethyl-1-pentene, 25% 2,4,4-trimethyl-2-pentene). The resulting solution is sucked into a stainless steel high-pressure reaction kettle. Crude phosphine is washed with 40% NaOH solution and then enters the freeze dryer, freeze-dried at 0-3°C to remove water, and then enters the high-pressure reaction pot through the compressor. The temperature in the pot is kept at -15~-20°C. When the pressure in the kettle rose to 70 atmospheres, open the vent valve to keep the pressure in the kettle. This process was maintained for 2 hours, and the input of crude phosphine gas was stopped. The pressure in the high-pressure reaction kettle was released to 40 atmospheres, and 1603 grams of phosphine was absorbed in the high-pressure reaction kettle (the total air flow rate was 3730 grams). Heat the high-pressure reaction pot and keep the temperature at 80-85°C, and the pressure in the pot rises to 60-7...
PUM
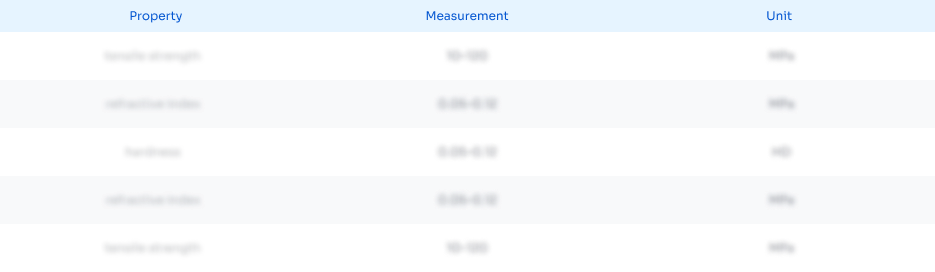
Abstract
Description
Claims
Application Information

- R&D
- Intellectual Property
- Life Sciences
- Materials
- Tech Scout
- Unparalleled Data Quality
- Higher Quality Content
- 60% Fewer Hallucinations
Browse by: Latest US Patents, China's latest patents, Technical Efficacy Thesaurus, Application Domain, Technology Topic, Popular Technical Reports.
© 2025 PatSnap. All rights reserved.Legal|Privacy policy|Modern Slavery Act Transparency Statement|Sitemap|About US| Contact US: help@patsnap.com