Method of cracking multi-production of trimethylbenzene with C9 and above heavyweight aromatic hydrocarbon ingredients
A technology for heavy aromatics and trimethylbenzene, applied in chemical instruments and methods, isomerization hydrocarbon production, distillation purification/separation, etc., can solve the difficulty of processing and harsh process, low content of trimethylbenzene, and cannot be transferred to produce BTX and trimethylbenzene Toluene and other issues
- Summary
- Abstract
- Description
- Claims
- Application Information
AI Technical Summary
Problems solved by technology
Method used
Image
Examples
Embodiment 1
[0024] Highly non-aromatic cracking C 9 + As raw material (toluene content is 3.1 tons / hour), using figure 1 craft technology. Reaction unit, reaction pressure 2.8 MPa, reaction temperature 340 °C, hydrogen partial pressure 1.14 MPa; stripping tower is a 44-layer float valve tray, the operating pressure at the top of the tower is 0.7 MPa, the control temperature of the top separator is 40 °C, discharge Non-condensable gas, in which the molar concentration of ethane is 23.3%, the molar concentration of propane is 63.3%, and other light hydrocarbons are 13.4mol%. The benzene tower adopts 55 layers of valve trays, the operating pressure at the top of the tower is 0.05MPa, and 8.4 tons / hour of benzene product with a purity of 99.95wt% is obtained at the top of the tower. The toluene tower adopts 55 layers of valve trays, the operating pressure at the top of the tower is 0.05MPa, and 14.2 tons / hour of toluene product with a purity of 99.9wt% is obtained at the top of the tower. ...
Embodiment 2
[0028] use C 9 And above heavy aromatics group cracking method to produce more trimethylbenzene, with the high non-aromatic cracking C after two-stage hydrogenation 9 + As the raw material (see Table 1 for the raw material conditions), the raw material is purified, mixed with hydrogen, heated to 300 ° C, and then enters a fixed-bed reactor equipped with a zeolite catalyst loaded with noble metal Zn for reaction to generate trimethylbenzene-rich aromatics and Reaction product of light alkane components. Reactor operating conditions: weight space velocity is 2h -1 , the hydrogen / hydrocarbon feedstock molar ratio is 2:1, the reaction inlet temperature is 380°C, and the reaction pressure is 4.5MPa.
[0029] The reaction product is condensed into a gas phase and a liquid phase. The gas phase product mainly contains low-carbon alkanes and hydrogen, and the liquid phase product contains non-aromatic hydrocarbons; the liquid phase product containing non-aromatic hydrocarbons enters...
Embodiment 3
[0032] Highly non-aromatic cracking C 9 + As raw material (toluene content is 3.0 tons / hour), using figure 1 craft technology. figure 1 C shown 9 In the process flow of decomposing heavy aromatics and producing more trimethylbenzenes, fresh raw material 1, hydrogen 2 and recycled raw material 3 enter the reaction unit Ⅰ, and the reaction product 4 enters the product separator Ⅱ for vapor-liquid separation, and the separated reaction liquid 6 Enter the stripping tower III, get LPG at the top of the stripping tower, the feed 8 of the BTX tower comes from the bottom of the stripping tower, extract BTX from the top of the BTX tower IV, and get mesitylene and para-trimethylbenzene at the top of the trimethylbenzene tower V , part of the heavy carbon nine and above components 3 are returned to the reaction system, and part of the trimethylbenzene is extracted from the tower kettle 12 .
[0033] Reaction unit, reaction pressure 2.8 MPa, reaction temperature 340°C, hydrogen partia...
PUM
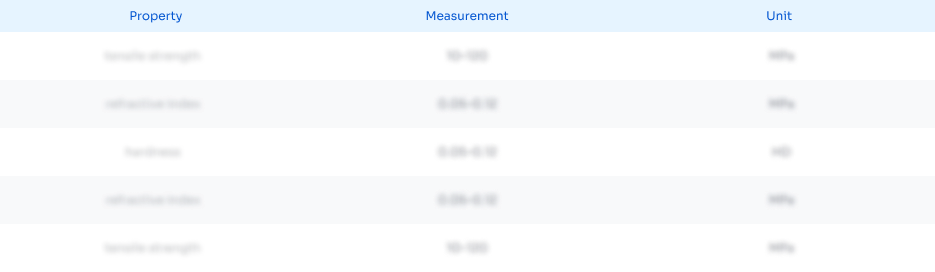
Abstract
Description
Claims
Application Information

- R&D
- Intellectual Property
- Life Sciences
- Materials
- Tech Scout
- Unparalleled Data Quality
- Higher Quality Content
- 60% Fewer Hallucinations
Browse by: Latest US Patents, China's latest patents, Technical Efficacy Thesaurus, Application Domain, Technology Topic, Popular Technical Reports.
© 2025 PatSnap. All rights reserved.Legal|Privacy policy|Modern Slavery Act Transparency Statement|Sitemap|About US| Contact US: help@patsnap.com