Novel dry-process cement kiln tail flue gas desulfurization system and desulfurization process thereof
A dry-process cement and desulfurization system technology, applied in separation methods, chemical instruments and methods, waste heat treatment, etc., can solve the problems of non-detection and high emission concentration, and achieve the effects of convenient operation, high desulfurization efficiency and short construction period
- Summary
- Abstract
- Description
- Claims
- Application Information
AI Technical Summary
Problems solved by technology
Method used
Image
Examples
Embodiment Construction
[0035] The specific implementation of the present invention will be described in further detail below by describing the embodiments with reference to the accompanying drawings, so as to help those skilled in the art have a more complete, accurate and in-depth understanding of the inventive concepts and technical solutions of the present invention.
[0036] like figure 2 The structure of the present invention expressed is a novel dry-process cement kiln tail gas desulfurization system. The dry-process cement kiln includes a decomposition furnace 6 , a humidifying tower 7 and a raw material mill 8 .
[0037] The new dry-process cement kiln is a rotary kiln 9. The novel dry-process cement kiln system of the present invention also includes a PH boiler 14, a high-temperature fan 18, a buffer bin 19, a confluence box 20, and an electric dust collector 21.
[0038] The invention belongs to cement clinker production line to reduce SO 2 Emission desulfurization technology. This tec...
PUM
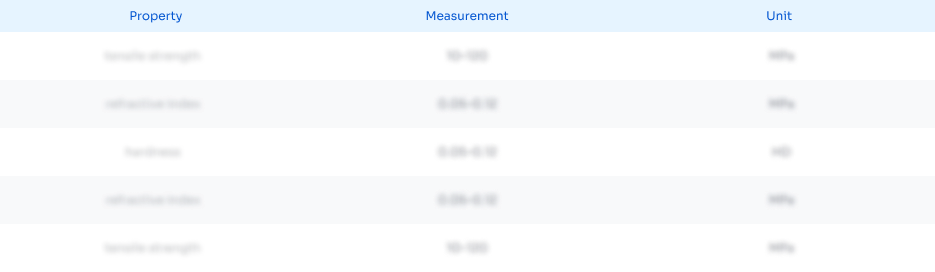
Abstract
Description
Claims
Application Information

- R&D
- Intellectual Property
- Life Sciences
- Materials
- Tech Scout
- Unparalleled Data Quality
- Higher Quality Content
- 60% Fewer Hallucinations
Browse by: Latest US Patents, China's latest patents, Technical Efficacy Thesaurus, Application Domain, Technology Topic, Popular Technical Reports.
© 2025 PatSnap. All rights reserved.Legal|Privacy policy|Modern Slavery Act Transparency Statement|Sitemap|About US| Contact US: help@patsnap.com