Preparation method of sodium carboxymethylcellulose
A technology of sodium carboxymethyl cellulose and alkali cellulose, which is applied in the field of chemical modification of natural polymers, can solve the problems of prolonging the production cycle, difficulty in meeting demands, and high production costs, and achieve loose production equipment requirements, reduce preparation costs, Good product performance
- Summary
- Abstract
- Description
- Claims
- Application Information
AI Technical Summary
Problems solved by technology
Method used
Image
Examples
Embodiment 1
[0087] In this example, a qualified low-viscosity sodium carboxymethylcellulose for drilling fluid was prepared by semi-dry method using wood pulp block as raw material.
[0088] (1) Preparation: Put the wood pulp block into a pulverizer and pulverize until the raw material changes from block to fluffy floc without hard core. Put the floc raw materials into an oven to dry.
[0089] Add 10 g of dried flocculent wood pulp raw material, 6.03 g of granular solid sodium hydroxide into the pulverizer, and then add 15.46 g of a 25% sodium hydroxide aqueous solution in the form of spraying. Start the pulverizer for 2min. After the pulverization is completed, put the pulverizer at room temperature for 20 minutes to complete an alkalization cycle. Then carry out the crushing-standstill alkalization process again, and repeat 3 cycles in total. The whole alkalization reaction time is 1.1h.
[0090] Add 13.5 g of solid monochloroacetic acid to the pulverizer at one time, and then start...
Embodiment 2
[0102] In this example, a qualified medium-viscosity sodium carboxymethylcellulose for drilling fluid was prepared by semi-dry method using wood pulp block as raw material. The main difference between this example and Example 1 is that: during the alkalization reaction, the amount of solid sodium hydroxide and sodium hydroxide solution is different; the time for a single operation of the pulverizer is different; the time for alkalization reaction and etherification reaction is different ; Chloroacetic acid was added twice in a ratio of 1:1.
[0103] (1) Preparation: Put the wood pulp block into a pulverizer and pulverize until the raw material changes from block to fluffy floc without hard core. Put the floc raw materials into an oven to dry.
[0104] Add 10 g of dried floc wood pulp raw material, 5.3 g of flaky solid sodium hydroxide into the pulverizer, and then add 17.85 g of a 25% sodium hydroxide aqueous solution in the form of dropwise addition. Start the pulverizer fo...
Embodiment 3
[0114] In this example, a qualified high-viscosity sodium carboxymethyl cellulose for drilling fluid was prepared by semi-dry method using wood pulp block as raw material. The main differences between this example and Example 1 are: in the alkalization process, the amount of solid sodium hydroxide and sodium hydroxide solution is different; the concentration of sodium hydroxide solution is different; the time of a single operation of the pulverizer is different; etherification The ambient temperature of the reaction is different; the total time of the etherification reaction is different; monochloroacetic acid is added twice in a ratio of 1:2.
[0115] (1) Preparation: Put the wood pulp block into a pulverizer and pulverize until the raw material changes from block to fluffy floc without hard core. Put the floc raw materials into an oven to dry.
[0116] Add 10 g of dried flocculent wood pulp raw material, 5.78 g of granular solid sodium hydroxide into the pulverizer, and the...
PUM
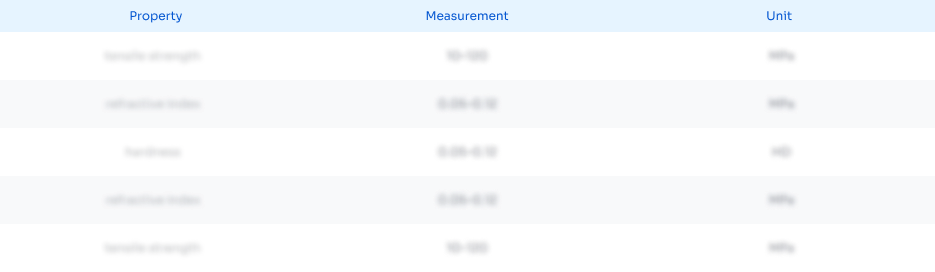
Abstract
Description
Claims
Application Information

- R&D Engineer
- R&D Manager
- IP Professional
- Industry Leading Data Capabilities
- Powerful AI technology
- Patent DNA Extraction
Browse by: Latest US Patents, China's latest patents, Technical Efficacy Thesaurus, Application Domain, Technology Topic, Popular Technical Reports.
© 2024 PatSnap. All rights reserved.Legal|Privacy policy|Modern Slavery Act Transparency Statement|Sitemap|About US| Contact US: help@patsnap.com