Direct aromatization process of pyridine derivative
A derivative and aromatization technology, which is applied in the field of preparation of aromatic pyridine derivatives, can solve the problems of expensive metal reagents, and achieve the effect of high reaction yield and low production cost
- Summary
- Abstract
- Description
- Claims
- Application Information
AI Technical Summary
Problems solved by technology
Method used
Examples
Embodiment 1
[0012] Aromatization of 4-cyanopyridine
[0013] In a 50mL three-necked flask, add 4mmol (0.42g) of 4-cyanopyridine, 4.4mmol (0.54g) of phenylboronic acid, 10mL of dichloromethane, 10mL of water, 0.4mmol of ferrous oxalate, 4mmol of trifluoroacetic acid (0.46 g; 306 μL), under stirring at room temperature (25°C), 12mmol (3.24g) of potassium peroxodisulfate was added, and stirring was continued for 24h at room temperature (25°C).
[0014] After the reaction, the obtained product was filtered, and the residue was washed 2-3 times with a small amount of dichloromethane (about 5 mL each time); after the combined dichloromethane solution, it was washed twice with 5% sodium bicarbonate aqueous solution; The dichloromethane solution was dried over magnesium sulfate over water, filtered with suction, and the filtrate was taken. The dichloromethane was removed from the obtained filtrate by rotary evaporation to obtain a crude product. The crude product is separated by ordinary silica ...
Embodiment 2
[0018] Aromatization of 4-cyanopyridine
[0019] In a 50mL three-necked flask, add 4mmol (0.42g) of 4-cyanopyridine, 4.4mmol (0.54g) of phenylboronic acid, 10mL of dichloromethane, 10mL of water, 0.4mmol of ferrous sulfide, 4mmol of trifluoroacetic acid (0.46g; 306μL ). Under stirring at room temperature (25°C), ammonium peroxodisulfate (2.74g) was added, and stirring was continued for 48h at room temperature (25°C).
[0020] After the reaction, the obtained product was filtered, and the residue was washed 2-3 times with a small amount of dichloromethane (about 5 mL each time); after the combined dichloromethane solution, it was washed twice with 5% sodium bicarbonate aqueous solution; The dichloromethane solution was dried over magnesium sulfate over water, and the filtrate was collected by suction filtration. The dichloromethane was removed from the filtrate by rotary evaporation to obtain a crude product. The crude product is separated by ordinary silica gel column (inclu...
Embodiment 3
[0022] Aromatization of 4-acetylpyridine
[0023] In a 50mL three-necked flask, add 4mmol (0.48g) of 4-acetylpyridine, 4.4mmol (0.54g) of phenylboronic acid, 10mL of dichloromethane, 10mL of water, 0.4mmol of ferrous oxalate, 4mmol of trifluoroacetic acid (0.46g; 306μL ). Under stirring at room temperature (25° C.), 12 mmol (3.24 g) of potassium peroxodisulfate was added, and stirring was continued for 24 h at this temperature.
[0024] After the reaction, filter the obtained product, and wash the residue with a small amount of dichloromethane 2-3 times (about 5 mL each time); after combining the obtained dichloromethane solution, wash twice with 5% sodium bicarbonate aqueous solution; Dry the dichloromethane solution with 2 g of anhydrous magnesium sulfate, filter the filtrate with suction, and remove the dichloromethane from the filtrate by rotary evaporation to obtain a crude product. The crude product is separated by ordinary silica gel column (containing 200-300 mesh si...
PUM
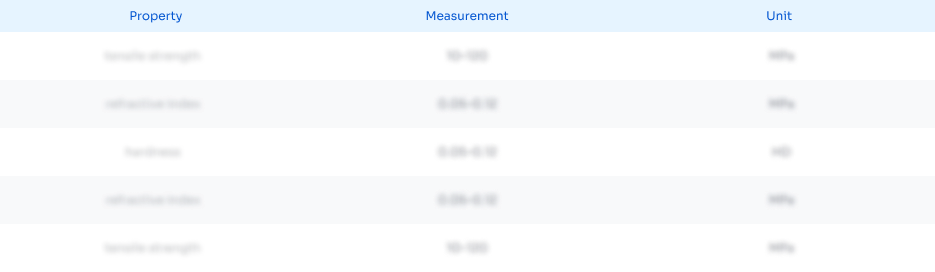
Abstract
Description
Claims
Application Information

- R&D Engineer
- R&D Manager
- IP Professional
- Industry Leading Data Capabilities
- Powerful AI technology
- Patent DNA Extraction
Browse by: Latest US Patents, China's latest patents, Technical Efficacy Thesaurus, Application Domain, Technology Topic, Popular Technical Reports.
© 2024 PatSnap. All rights reserved.Legal|Privacy policy|Modern Slavery Act Transparency Statement|Sitemap|About US| Contact US: help@patsnap.com