Multi-purpose ammonium-free fluxing agent for hot dip coating and application method thereof
A technology of flux and hot-dip plating, which is applied in hot-dip plating process, metal material coating process, coating, etc., and can solve problems that have not been applied
- Summary
- Abstract
- Description
- Claims
- Application Information
AI Technical Summary
Problems solved by technology
Method used
Image
Examples
Embodiment 1
[0024] Example 1: Take 300g of zinc chloride, 24g of sodium chloride, 12g of calcium chloride, 60g of stannous chloride, and 60g of potassium fluorozirconate, add 1L of water to prepare a plating flux solution, heat the solution to 70°C, and stir thoroughly during the heating process uniform. Immerse the Q235 steel sheet with the size of 50×50×2mm that has been washed by alkali cleaning, degreasing, pickling and rust removal in the fluxing solution for 4 minutes, and then take the Q235 steel sheet out of the fluxing solution, at a temperature of 120 Dry in a drying oven at ℃ for 4 minutes, then immerse in Galvalume molten pool for hot-dip plating, no zinc explosion occurs during immersion, a small amount of smoke and dust are generated on the surface of the molten pool, and there are floating black oxides on the surface of the molten pool; the dipping is completed Finally, the Q235 steel sheet was slowly lifted out of the molten pool and then quickly water-cooled. It was fou...
Embodiment 2
[0025] Example 2: Take 240g of zinc chloride, 10g of sodium chloride, 5g of calcium chloride, 20g of stannous chloride, and 16g of potassium fluorozirconate, add 1L of water to prepare a plating flux solution, heat the solution to 70°C, and stir thoroughly during the heating process uniform. Immerse the Q235 steel sheet with the size of 50×50×2mm that has been washed by alkali cleaning, degreasing, pickling and rust removal in the fluxing solution for 4 minutes, and then take the Q235 steel sheet out of the fluxing solution, at a temperature of 120 Dry in a drying oven at ℃ for 4 minutes, then immerse in Galvalume molten pool for hot-dip plating, no zinc explosion occurs during immersion, a small amount of smoke and dust are generated on the surface of the molten pool, and there are floating black oxides on the surface of the molten pool; after dipping is completed The Q235 steel sheet was slowly lifted out of the molten pool and then quickly water-cooled. It was found that ...
Embodiment 3
[0026] Example 3: Take 300g of zinc chloride, 20g of sodium chloride, 10g of calcium chloride, 40g of stannous chloride, and 50g of potassium fluorozirconate, add 1L of water to prepare a plating flux solution, heat the solution to 70°C, and stir thoroughly during the heating process uniform. After the Q235 steel sheet with the size of 50×50×2mm is degreased by alkali, pickled and derusted by pickling, and then rinsed, it is immersed in the flux solution for 4 minutes, then taken out of the flux solution, and placed in a drying oven at a temperature of 120°C. Dry in the middle for 4 minutes, then dip into the pure zinc molten pool for hot-dip plating, no zinc explosion occurs during immersion, a small amount of smoke and dust are generated on the surface of the molten pool, and there are floating black oxides on the surface of the molten pool; after the dipping is completed, the Q235 steel sheet After being slowly lifted from the molten pool, it was quickly water-cooled. It ...
PUM
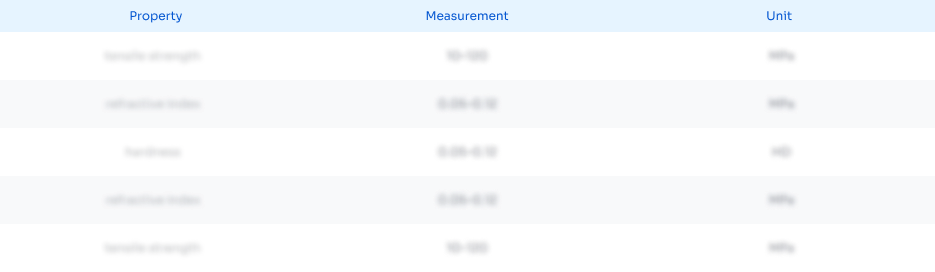
Abstract
Description
Claims
Application Information

- R&D Engineer
- R&D Manager
- IP Professional
- Industry Leading Data Capabilities
- Powerful AI technology
- Patent DNA Extraction
Browse by: Latest US Patents, China's latest patents, Technical Efficacy Thesaurus, Application Domain, Technology Topic, Popular Technical Reports.
© 2024 PatSnap. All rights reserved.Legal|Privacy policy|Modern Slavery Act Transparency Statement|Sitemap|About US| Contact US: help@patsnap.com