Method for manufacturing dyed leather based on aqueous resin and dyed leather
A manufacturing method and technology for dyeing leather, which is applied in dyeing methods, chemical instruments and methods, textiles and papermaking, etc., can solve the problems that cannot meet the requirements of ecological synthetic leather, etc., and achieve the goal of eliminating fire hazards, clear layering, and adding new varieties Effect
- Summary
- Abstract
- Description
- Claims
- Application Information
AI Technical Summary
Problems solved by technology
Method used
Examples
Embodiment 1
[0027] Embodiment 1: the manufacture of dyed garment leather
[0028] (1) Preparation of water-based polyurethane veneer paste and three-plate surface paste:
[0029] (a) Preparation of water-based polyurethane facing layer slurry
[0030] Mix the water-based anionic surface layer with a modulus of about 40Mpa with 100 parts of polyurethane, 0.2 parts of water-based silicone leveling agent, 0.1 part of water-based silicone defoamer, and 0.3 parts of water-based polyurethane thickener, and the viscosity is 2500 mPa .s or so (temperature 25 ℃, the same below) veneer paste;
[0031] (b) Preparation of slurry at the third version table
[0032] Mix 100 parts of water-based cationic matting polyurethane with a modulus of 40Mpa, 0.2 parts of water-based polyurethane thickener, and 0.2 parts of water-based silicone leveling agent to prepare a three-plate surface slurry with a viscosity of 800-1000 mPa.s;
[0033] (2) Manufacture of dyed leather: adopt the transfer coating process,...
Embodiment 2
[0040] Embodiment 2: the manufacture of dyed sofa leather
[0041] (1) Preparation of water-based polyurethane veneer paste and three-plate surface paste:
[0042] (a) Preparation of water-based polyurethane facing layer slurry
[0043] Mix the water-based anionic surface layer with a modulus of about 60Mpa with 100 parts of polyurethane, 0.3 parts of water-based silicone leveling agent, 0.2 parts of water-based silicone defoamer, and 0.3 parts of water-based polyurethane thickener, and the viscosity is 3000 mPa .s or so (temperature 25 ℃, the same below) veneer paste;
[0044] (b) Preparation of slurry at the third version table
[0045] Mix 100 parts of water-based cationic matting polyurethane with a modulus of 50Mpa, 0.2 parts of water-based polyurethane thickener, and 0.2 parts of water-based silicone leveling agent to prepare a three-plate surface slurry with a viscosity of 800-1000 mPa.s;
[0046] (2) Manufacture of dyed leather: adopt the transfer coating process, t...
Embodiment 3
[0053] Example 3: Manufacture of Dyed Boot Leather
[0054] (1) Preparation of water-based polyurethane veneer paste and three-plate surface paste:
[0055] (a) Preparation of water-based polyurethane facing layer slurry
[0056] Mix the water-based anionic surface layer with a modulus of about 45Mpa with 100 parts of polyurethane, 0.4 parts of water-based silicone leveling agent, 0.3 parts of water-based silicone defoamer, and 0.3 parts of water-based polyurethane thickener, and the viscosity is 2600 mPa .s or so (temperature 25 ℃, the same below) veneer paste;
[0057] (b) Preparation of slurry at the third version table
[0058] Mix 100 parts of water-based cationic matting polyurethane with a modulus of 50Mpa, 0.2 parts of water-based polyurethane thickener, and 0.2 parts of water-based silicone leveling agent to prepare a three-plate surface slurry with a viscosity of 800 mPa.s;
[0059] (2) Manufacture of dyed leather: adopt the transfer coating process, that is, appl...
PUM
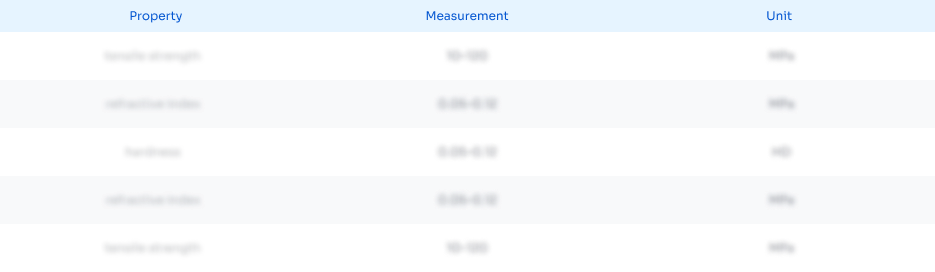
Abstract
Description
Claims
Application Information

- R&D
- Intellectual Property
- Life Sciences
- Materials
- Tech Scout
- Unparalleled Data Quality
- Higher Quality Content
- 60% Fewer Hallucinations
Browse by: Latest US Patents, China's latest patents, Technical Efficacy Thesaurus, Application Domain, Technology Topic, Popular Technical Reports.
© 2025 PatSnap. All rights reserved.Legal|Privacy policy|Modern Slavery Act Transparency Statement|Sitemap|About US| Contact US: help@patsnap.com