Preparation method and application of a moisture-absorbing and perspiration-wicking and quick-drying finishing agent for nylon or nylon/spandex fabrics
A technology of moisture absorption and perspiration, finishing agent, applied in the direction of fiber processing, textile and papermaking, fiber type, etc., can solve the problem that the finishing agent has poor washability, hydrophilic performance and hand feel cannot reach high-end products, and cannot be higher than clothing. requirements and other issues, to achieve excellent hydrophilic and hygroscopic properties, good washability, and increased added value.
- Summary
- Abstract
- Description
- Claims
- Application Information
AI Technical Summary
Problems solved by technology
Method used
Image
Examples
Embodiment 1
[0028] The reaction kettle is dried to remove water, and 300Kg EO / PO block polyether glycol (molecular weight: 1950) is injected. The temperature is slowly raised to 120°C to remove water under reduced pressure for 2h, and the temperature is reduced to 30-40°C. Slowly add 41Kg diisocyanate IPDI, and increase the temperature. After reacting at 80℃ for 2h, slowly add 7.1Kg of capping agent methyl isobutyl ketoxime and react at 80~85℃ for 4h, cooling to obtain a colorless and transparent capped thermally reactive polyurethane prepolymer, and cooling to 40 Add 200Kg of diethylene glycol monobutyl ether, 150Kg of stearic acid polyoxyethylene ether (9EO), 301.9Kg of deionized water at ℃, and stir to get it.
Embodiment 2
[0030] The reaction kettle is dried to remove water, and 300Kg EO / PO block polyether glycol (molecular weight: 1950) is injected. The temperature is slowly raised to 120°C to remove water under reduced pressure for 1h, and the temperature is reduced to 30-40°C. 46.2Kg of diphenylmethane is slowly added Diisocyanate MDI, heated to 80℃ and reacted for 2h, slowly added 2.7Kg of blocking agent methyl ethyl ketoxime, reacted at 80~85℃ for 4h, cooled to obtain a colorless and transparent blocked thermoreactive polyurethane prepolymer, and cooled to 40 Add 200Kg of diethylene glycol monobutyl ether, 100Kg of polyether hydrophilic silicone oil, and 351.1Kg of deionized water at ℃, and stir to get it.
Embodiment 3
[0032] The reaction kettle is dried and dewatered, and 300Kg EO / PO block polyether glycol (molecular weight 1950) is injected. The temperature is slowly raised to 120°C to remove water under reduced pressure for 2h, and the temperature is lowered to 30-40°C. 31Kg diisocyanate HDI is slowly added, and the temperature is raised After reacting at 80℃ for 2h, slowly add 7.0Kg of end-capping agent cyclohexanone oxime, react at 85℃ for 4h, and cool to obtain a colorless and transparent end-capped thermoreactive polyurethane prepolymer. When the temperature is lowered to 40℃, add 200Kg Glycol monobutyl ether, stearic acid polyoxyethylene ether (9EO) 150Kg, deionized water 312Kg, stir well to get.
PUM
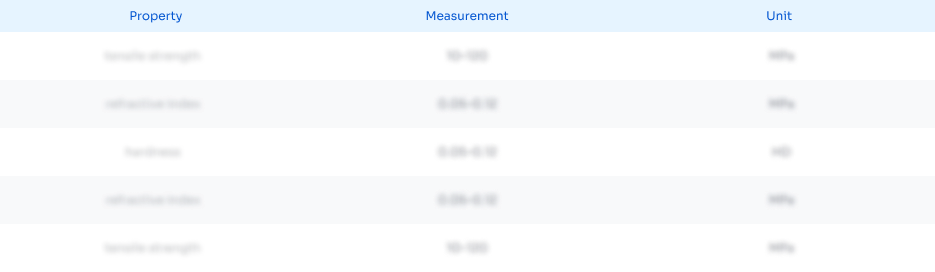
Abstract
Description
Claims
Application Information

- R&D Engineer
- R&D Manager
- IP Professional
- Industry Leading Data Capabilities
- Powerful AI technology
- Patent DNA Extraction
Browse by: Latest US Patents, China's latest patents, Technical Efficacy Thesaurus, Application Domain, Technology Topic, Popular Technical Reports.
© 2024 PatSnap. All rights reserved.Legal|Privacy policy|Modern Slavery Act Transparency Statement|Sitemap|About US| Contact US: help@patsnap.com