Antistatic fiber and preparation method thereof
A technology of antistatic fiber and mass fraction, applied in the direction of conductive/antistatic filament manufacturing, melt spinning, conjugated synthetic polymer artificial filament, etc., can solve the problems of not widely used, weakened and disappeared antistatic properties problems, to achieve the effect of wide application, permanent and effective antistatic performance, easy weaving and dyeing
- Summary
- Abstract
- Description
- Claims
- Application Information
AI Technical Summary
Problems solved by technology
Method used
Examples
Embodiment 1
[0013] Antistatic fiber, prepared by melt spinning the following raw materials in parts by mass: 30 parts of polyethylene terephthalate, 10 parts of polypropylene, 1 part of polytetrafluoroethylene, 1 part of glyceryl monostearate 0.1 part of lanolin wax polyoxypropylene ether, 2 parts of nano-titanium dioxide.
[0014] The preparation method of the antistatic fiber comprises the following steps: mixing polyethylene terephthalate, polypropylene, polytetrafluoroethylene, glyceryl monostearate, lanolin wax polyoxypropylene ether and nano Titanium dioxide was vacuum-dried at 30°C for 3 hours. After being melted and extruded, it was transported to a spinning box at a spinning temperature of 232°C. The melted yarn was cooled, drawn, and shaped to obtain antistatic fibers.
Embodiment 2
[0016] Antistatic fiber, prepared by melt spinning the following raw materials in parts by mass: 40 parts of polyethylene terephthalate, 15 parts of polypropylene, 1.5 parts of polytetrafluoroethylene, 2 parts of glyceryl monostearate part, 0.2 part of lanolin wax polyoxypropylene ether, and 3 parts of nano-titanium dioxide.
[0017] The preparation method of the antistatic fiber comprises the following steps: mixing polyethylene terephthalate, polypropylene, polytetrafluoroethylene, glyceryl monostearate, lanolin wax polyoxypropylene ether and nano Titanium dioxide was vacuum-dried at 30°C for 3 hours. After being melted and extruded, it was transported to a spinning box at a spinning temperature of 232°C. The melted yarn was cooled, drawn, and shaped to obtain antistatic fibers.
Embodiment 3
[0019] Antistatic fiber, prepared by melt spinning the following raw materials in parts by mass: 34 parts of polyethylene terephthalate, 12 parts of polypropylene, 1.2 parts of polytetrafluoroethylene, 1.8 parts of glyceryl monostearate part, 0.16 part of lanolin wax polyoxypropylene ether, and 2.6 parts of nano-titanium dioxide.
[0020] The preparation method of the antistatic fiber comprises the following steps: mixing polyethylene terephthalate, polypropylene, polytetrafluoroethylene, glyceryl monostearate, lanolin wax polyoxypropylene ether and nano Titanium dioxide was vacuum-dried at 30°C for 3 hours. After being melted and extruded, it was transported to a spinning box at a spinning temperature of 232°C. The melted yarn was cooled, drawn, and shaped to obtain antistatic fibers.
PUM
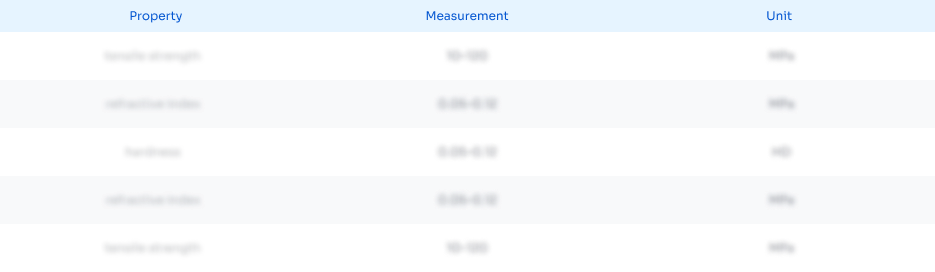
Abstract
Description
Claims
Application Information

- R&D
- Intellectual Property
- Life Sciences
- Materials
- Tech Scout
- Unparalleled Data Quality
- Higher Quality Content
- 60% Fewer Hallucinations
Browse by: Latest US Patents, China's latest patents, Technical Efficacy Thesaurus, Application Domain, Technology Topic, Popular Technical Reports.
© 2025 PatSnap. All rights reserved.Legal|Privacy policy|Modern Slavery Act Transparency Statement|Sitemap|About US| Contact US: help@patsnap.com