Grinding method for machining high-precision outer spherical surface through ordinary cylindrical grinding machine
A cylindrical grinding machine and grinding processing technology, applied in the field of mechanical processing, can solve the problems of low efficiency, high value, difficult to guarantee accuracy, etc., and achieve the effects of simple manufacturing, small investment and improved production efficiency
- Summary
- Abstract
- Description
- Claims
- Application Information
AI Technical Summary
Problems solved by technology
Method used
Image
Examples
Embodiment Construction
[0033] An example is given below for further details. The size is a recommended value, not a strict limit. Assuming the part size is like figure 1 Shown:
[0034] First, choose a grinding wheel.
[0035] The width of the grinding wheel must be greater than the width of the part (14-16mm). The diameter of the grinding wheel must be enough to grind the spherical surface of the sphere, that is, the thickness of the grinding wheel from the outer diameter to the mounting hole must be greater than the depth of the sphere, that is, the vertical distance from the vertex of the sphere to the chord length of the sphere. The formula is:
[0036] ( 80 - 0.005 0 ÷ 2 ) - ( 80 - 0.005 0 ÷ 2 ) 2 - ( 56 ÷ 2 ) 2 = 3 9.99875 - 28 . 56396 = 11.43479 ≈ 11.435 mm .
[0037] Considering the dressing and regrinding of the grinding wheel, the width and diameter of the grinding wheel should be larg...
PUM
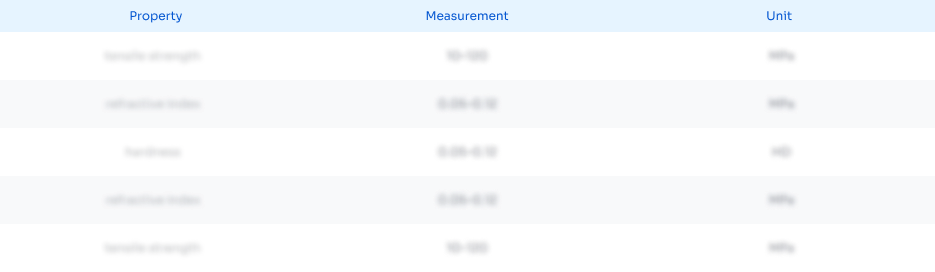
Abstract
Description
Claims
Application Information

- R&D
- Intellectual Property
- Life Sciences
- Materials
- Tech Scout
- Unparalleled Data Quality
- Higher Quality Content
- 60% Fewer Hallucinations
Browse by: Latest US Patents, China's latest patents, Technical Efficacy Thesaurus, Application Domain, Technology Topic, Popular Technical Reports.
© 2025 PatSnap. All rights reserved.Legal|Privacy policy|Modern Slavery Act Transparency Statement|Sitemap|About US| Contact US: help@patsnap.com