A preparation method of high-alumina bricks for slurry-bonded matrix homogenization blast furnace
A high-alumina brick and mud technology, applied in the field of refractory materials, can solve problems such as energy consumption and waste of resources, and achieve the effects of energy saving, stable performance and cost reduction
- Summary
- Abstract
- Description
- Claims
- Application Information
AI Technical Summary
Problems solved by technology
Method used
Image
Examples
Embodiment 1
[0014] The high-alumina bricks used in slurry-bonded matrix homogenization blast furnaces use the following raw materials in parts by weight: 10 parts of special-grade high-alumina bauxite clinker, 10 parts of first-grade high-alumina bauxite clinker, 20 parts of co-grinding powder A, and 5 parts of mud.
[0015] The components of the co-grinding powder A in parts by weight are: 40 parts of special-grade high-alumina bauxite clinker, 20 parts of special-grade high-alumina bauxite raw meal, 1 part of coal gangue, and 5 parts of soft clay.
[0016] The mud is made by ball milling Guangxi clay, coal gangue, lignin and water with a mass ratio of 0.5:0.5:0.5:2.
[0017] The method for preparing slurry-bonded matrix homogenized high-alumina bricks for blast furnaces includes the following steps: 1) adding Guangxi clay, coal gangue, lignin, and water with a mass ratio of 0.5:0.5:0.5:2 to a ball mill and ball milling for 7 hours to form a slurry ;
[0018] 2) Mill the super-grade hig...
Embodiment 2
[0022] The high-alumina bricks used in the slurry-bonded matrix homogenization blast furnace, the raw materials used in parts by weight are: 20 parts of super-grade high-alumina bauxite clinker, 30 parts of first-grade high-alumina bauxite clinker, 5 parts of andalusite, 50 parts of co-grinding powder A, mud 8 servings.
[0023] The components of the co-grinding powder A in parts by weight are: 50 parts of special-grade high-alumina bauxite clinker, 30 parts of special-grade high-alumina bauxite raw meal, 5 parts of coal gangue, and 10 parts of soft clay.
[0024] The mud is made by ball milling Guangxi clay, coal gangue, lignin and water with a mass ratio of 0.5:0.5:0.5:2.
[0025] The method for preparing slurry-bonded matrix homogenized high-alumina bricks for blast furnaces includes the following steps: 1) adding Guangxi clay, coal gangue, lignin, and water with a mass ratio of 0.5:0.5:0.5:2 to a ball mill and ball milling for 8 hours to form a slurry ;
[0026] 2) Mill ...
Embodiment 3
[0030] The high-alumina bricks used in the mud-bonded matrix homogenization blast furnace, the raw materials used in parts by weight are: 30 parts of super-grade high-alumina bauxite clinker, 10 parts of first-grade high-alumina bauxite clinker, 10 parts of andalusite, 20 parts of co-grinding powder A, mud 6 servings.
[0031] The components of co-grinding powder A in parts by weight are: 60 parts of super-grade high-alumina bauxite clinker, 20 parts of super-grade high-alumina bauxite raw meal, 8 parts of coal gangue, and 5 parts of soft clay.
[0032] The mud is made by ball milling Guangxi clay, coal gangue, lignin and water with a mass ratio of 0.5:0.5:0.5:2.
[0033] The method for preparing slurry-bonded matrix homogenized high-alumina bricks for blast furnaces includes the following steps: 1) adding Guangxi clay, coal gangue, lignin, and water with a mass ratio of 0.5:0.5:0.5:2 to a ball mill and ball milling for 9 hours to form a slurry ;
[0034] 2) Mill the super-g...
PUM
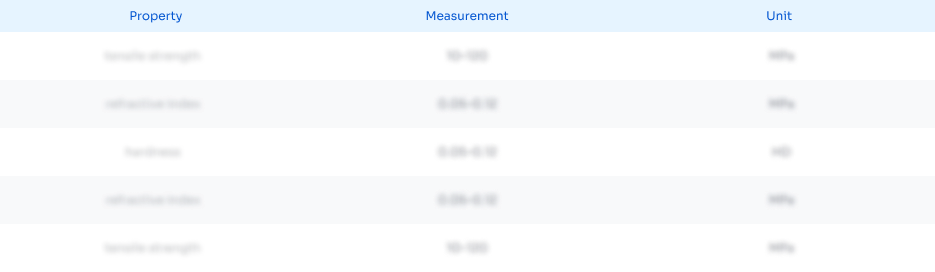
Abstract
Description
Claims
Application Information

- Generate Ideas
- Intellectual Property
- Life Sciences
- Materials
- Tech Scout
- Unparalleled Data Quality
- Higher Quality Content
- 60% Fewer Hallucinations
Browse by: Latest US Patents, China's latest patents, Technical Efficacy Thesaurus, Application Domain, Technology Topic, Popular Technical Reports.
© 2025 PatSnap. All rights reserved.Legal|Privacy policy|Modern Slavery Act Transparency Statement|Sitemap|About US| Contact US: help@patsnap.com