In situ synthesis method for Gd2Zr2O7/ZrO2(3Y) nano-powder
A nanopowder, in-situ synthesis technology, applied in nanotechnology, nanotechnology, nanotechnology for materials and surface science, etc.
- Summary
- Abstract
- Description
- Claims
- Application Information
AI Technical Summary
Problems solved by technology
Method used
Image
Examples
Embodiment 1
[0024] Will Gd 2 o 3 , ZrOCl 2 .8H 2 O, Y 2 o 3 The raw materials are weighed according to the precise chemical ratio and dissolved in HNO 3 Prepare a rare earth mixed solution with an initial mother salt solution concentration of 0.05 mol / L, and at the same time prepare a pH=11.0 ammonia solution with a concentration of 0.5 mol / L as a precipitant, use in-situ reverse titration, and use a peristaltic pump to remove the precipitant Drop into the mother salt solution, and at the same time, use a magnetic device to continuously stir the precursor precipitate for 1 to 4 hours to complete the reaction and achieve uniform dispersion. Finally, a white flocculent precipitate was obtained. After aging for 24 h, the precursor precipitate was washed three times with deionized water to remove impurity ions, and then washed twice with absolute ethanol. After filtering, it was dried in a vacuum oven at 60°C for 24 hours. Gd was prepared by wet ball milling for 12 hours, and then calci...
Embodiment 2
[0026] Be prepared with the rare earth mixed solution that the initial mother salt solution concentration is 0.10 mol / L, other conditions are as embodiment 1, such as Figure 4 As shown, the agglomeration of the powder is serious, and the particle size difference is large, and the particle size is about 240nm.
Embodiment 3
[0028] Be prepared with the rare earth mixed solution that the initial mother salt solution concentration is 0.15 mol / L, other conditions are as embodiment 1, such as Figure 5 As shown, the powder agglomeration is obvious, the size of the particles is uneven, and the particle size is about 280nm.
PUM
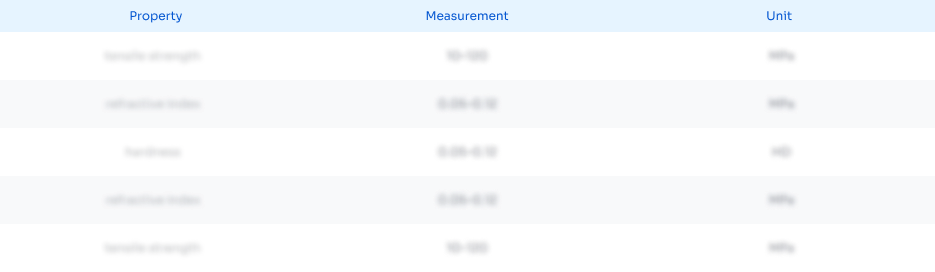
Abstract
Description
Claims
Application Information

- R&D
- Intellectual Property
- Life Sciences
- Materials
- Tech Scout
- Unparalleled Data Quality
- Higher Quality Content
- 60% Fewer Hallucinations
Browse by: Latest US Patents, China's latest patents, Technical Efficacy Thesaurus, Application Domain, Technology Topic, Popular Technical Reports.
© 2025 PatSnap. All rights reserved.Legal|Privacy policy|Modern Slavery Act Transparency Statement|Sitemap|About US| Contact US: help@patsnap.com