A processing method of elastic collets for three-dimensional corner clamping pipes in a numerically controlled pipe bending machine
An elastic collet and three-dimensional technology, which is applied in the field of CNC pipe bending machining, can solve the problems of easy damage to the workpiece surface, insufficient elasticity of the elastic collet, and low service life, and achieve the effects of low cost, increased elasticity, and long life
- Summary
- Abstract
- Description
- Claims
- Application Information
AI Technical Summary
Problems solved by technology
Method used
Image
Examples
Embodiment 1
[0042] Such as figure 1 , figure 2 and image 3 As shown, a processing method of a three-dimensional three-dimensional corner clamping collet in a numerically controlled pipe bending machine, the steps are:
[0043] (1) Raw material preparation for forging blank
[0044] Casting into a cylindrical forging blank, the mass percentage of forging blank components is: C: 0.50%, Mn: 0.55%, Si: 2.05%, S: ≤0.025%, P: ≤0.025%, Cr: ≤0.30%, Ni : ≤0.25%, Y 2 o 3 : 0.06%, the balance is Fe;
[0045] (2) Annealing treatment of forging blank
[0046] Annealing the forged blank obtained in step (1) through an annealing furnace, the annealing temperature is 860°C, the annealing time is 4h, and air cooling is carried out after cooling to 380°C in the annealing furnace;
[0047] (3) Initial processing of forging blanks
[0048] The forging blank in step (2) is first subjected to forging treatment, the initial forging temperature of forging is 1100-1200°C, the final forging temperature is ...
Embodiment 2
[0057] Same as Example 1, the difference is that the mass percentages of forged blank components are: C: 0.48%, Mn: 0.58%, Si: 1.93%, S: ≤0.025%, P: ≤0.025%, Cr: ≤0.30% , Ni: ≤0.25%, Y 2 o 3 : 0.07%, the balance is Fe; in the step (2), the annealing temperature is 840 ℃, and the annealing time is 5h, and air cooling is carried out after being cooled to 300 ℃ in the annealing furnace; in the step (6), the heat treatment of the collet, first Heat to 300°C and hold for 30 minutes, then heat to 530°C and hold for 60 minutes, then heat to 730°C, hold for 10 minutes, then heat to 920°C, hold for 60 minutes, first air cool to 700°C, then oil quench, then temper twice, Each tempering temperature was 470 and 495°C, respectively. The service life is 31158 times.
Embodiment 3
[0059] Same as Example 1, the difference is that the mass percentage of forging blank components is: C: 0.51%, Mn: 0.53%, Si: 2.12%, S: ≤0.025%, P: ≤0.025%, Cr: ≤0.30% , Ni: ≤0.25%, Y 2 o 3 : 0.05%, the balance is Fe; in the step (2), the annealing temperature is 870 DEG C, and the annealing time is 3h, and air cooling is carried out after being cooled to 450 DEG C in the annealing furnace; in the step (6), the heat treatment of the collet, first Heat to 420°C and hold for 20 minutes, then heat to 680°C and hold for 30 minutes, then heat to 670°C, hold for 20 minutes, then heat to 890°C, hold for 120 minutes, first air cool to 540°C, then oil quench, then temper twice, Each tempering temperature is 450 and 510°C respectively. The service life is 30073 times.
PUM
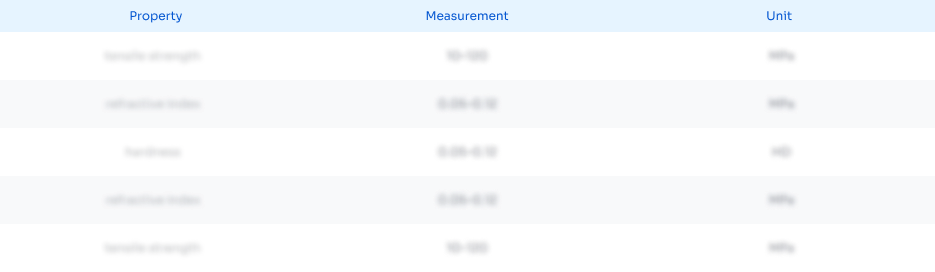
Abstract
Description
Claims
Application Information

- R&D
- Intellectual Property
- Life Sciences
- Materials
- Tech Scout
- Unparalleled Data Quality
- Higher Quality Content
- 60% Fewer Hallucinations
Browse by: Latest US Patents, China's latest patents, Technical Efficacy Thesaurus, Application Domain, Technology Topic, Popular Technical Reports.
© 2025 PatSnap. All rights reserved.Legal|Privacy policy|Modern Slavery Act Transparency Statement|Sitemap|About US| Contact US: help@patsnap.com