Multilayer coil part
A technology of stacking coils and components, applied in transformer/inductor components, electrical components, transformer/inductor coils/windings/connections, etc., can solve problems such as inductance reduction and inability to obtain DC superposition characteristics
- Summary
- Abstract
- Description
- Claims
- Application Information
AI Technical Summary
Problems solved by technology
Method used
Image
Examples
Embodiment 1
[0099] (production of samples)
[0100] [Magnet production]
[0101] As a ferrite raw material, prepare Fe 2 o 3 , Mn 2 o 3 , ZnO, NiO, and CuO, according to the composition of Table 1, weigh these ceramic raw materials. That is, take Fe 2 o 3 : 46.5mol%, Mn 2 o 3 : 2.5mol%, ZnO: 30.0mol%, CuO varies from 0.0 to 8.0mol%, and the rest is adjusted by NiO.
[0102] [Table 1]
[0103]
[0104] Next, these weighed objects were put into a ball mill made of vinyl chloride together with pure water and PSZ balls, thoroughly mixed and pulverized by a wet method, evaporated and dried, and then calcined at a temperature of 850°C.
[0105] Next, these pre-fired products are put into a ball mill made of vinyl chloride together with polyvinyl butyral-based binder (organic binder), ethanol (organic solvent), and PSZ balls, and are thoroughly mixed and pulverized. Get a slurry.
[0106] Next, the slurry was shaped into a sheet with a thickness of 25 μm using a doctor blade metho...
Embodiment 2
[0139] Fe ready to form the main component of the ferrite material 2 o 3 , Mn 2 o 3 , ZnO, NiO, and CuO, and SnO as a subcomponent material 2 . Then Fe 2 o 3 : 46.5mol%, Mn 2 o 3 : 2.5mol%, ZnO: 30.0mol%, CuO: 1.0mol%, and NiO: 20.0mol% were weighed, and SnO was further weighed at 0.0 to 3.0 parts by weight relative to 100 parts by weight of the main component. 2 .
[0140] Except for this, the samples of sample numbers 11-14 were produced according to the method and procedure similar to Example 1.
[0141] Next, for each of the samples of sample numbers 11 to 14, the content weight and average crystal grain size of CuO were measured, and a thermal shock test and a DC superposition test were performed.
[0142] Table 3 shows the measurement results of each sample of sample numbers 11-14.
[0143] [table 3]
[0144]
[0145] It is obvious from sample numbers 11 to 14 that there is basically no difference in the inductance change rate ΔL in the thermal shock test,...
PUM
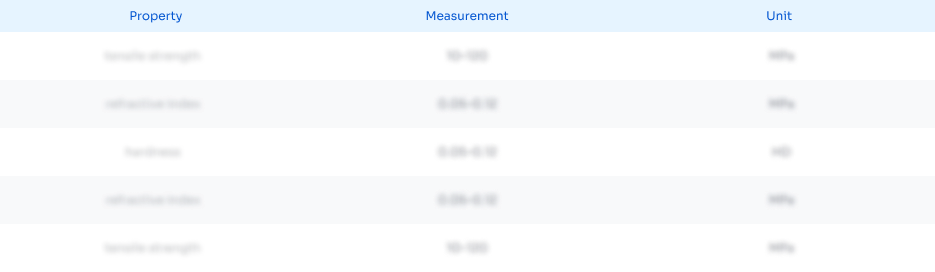
Abstract
Description
Claims
Application Information

- R&D
- Intellectual Property
- Life Sciences
- Materials
- Tech Scout
- Unparalleled Data Quality
- Higher Quality Content
- 60% Fewer Hallucinations
Browse by: Latest US Patents, China's latest patents, Technical Efficacy Thesaurus, Application Domain, Technology Topic, Popular Technical Reports.
© 2025 PatSnap. All rights reserved.Legal|Privacy policy|Modern Slavery Act Transparency Statement|Sitemap|About US| Contact US: help@patsnap.com