Magnesium sulfate preparation system
A magnesium sulfate and pulping technology, applied in the direction of magnesium sulfate, etc., can solve the problems of crystal slurry transportation pipeline blockage, increase the floor area of the device, increase the floor area, etc., to reduce system energy consumption, avoid pipeline blockage, The effect of saving floor space
- Summary
- Abstract
- Description
- Claims
- Application Information
AI Technical Summary
Problems solved by technology
Method used
Image
Examples
Embodiment 1
[0056] Step 1: Add magnesium oxide powder to high-temperature condensed water from an evaporator at 60°C to make a magnesium hydroxide slurry, and pump it to the absorption tower.
[0057] Step 2: Control the oxygen content of the flue gas before desulfurization in Table 1 to 18% by using the flue gas oxygen content regulating device.
[0058] Step 3: The flue gas velocity at the entrance of the absorption tower is 3m / s, and the flue gas temperature at the entrance is 120°C. The pH value of the slurry tank area at the bottom of the absorption tower is controlled to fluctuate between 6 and 7 to obtain a magnesium sulfate solution.
[0059] Step 4: pass the magnesium sulfate solution through a precision filter of no less than 300 mesh filter media to achieve fine filtration of the magnesium sulfate solution.
[0060]Step 5: Set the temperature at 30°C and the density at 1.2t / m 3 The magnesium sulfate solution is sent to the three-effect evaporator for evaporation to obtain a t...
Embodiment 2
[0073] Under the same working conditions as in Example 1, step 2: utilize the flue gas oxygen content regulating device to control the flue gas oxygen content before desulfurization respectively at 23%, the desulfurization effect obtained and the magnesium sulfate output are as follows:
[0074] Table 423% Oxygen Desulfurization Project Emissions and Magnesium Sulfate Output
[0075] serial number
project
quantity
unit
1
Flue gas volume at the outlet of the desulfurization unit (working condition)
1384210
m 3 / h
2
exhaust temperature
50
℃
3
SO 2 emission concentration
<40
mg / Nm 3
4
Magnesium sulfate output
4.5
t / h
5
>98
% mass percentage
[0076] Magnesium sulfate quality and its test method are the same as in Table 3.
[0077] It can be seen from Examples 1 to 2 that the present invention utilizes the method for preparing...
Embodiment 3
[0079] Step 1: Add magnesium oxide powder to the condensed water of the boiler evaporation system at 60°C to make magnesium hydroxide slurry, and pump it to the absorption tower.
[0080] Step 2: Control the oxygen content of the flue gas before desulfurization in Table 5 at 18% by using the flue gas oxygen content regulating device.
[0081] Step 3: The flue gas velocity at the entrance of the absorption tower is 3m / s, and the temperature of the flue gas at the entrance is 118°C. The pH value of the slurry tank area at the bottom of the absorption tower is controlled to fluctuate between 6 and 7 to obtain a magnesium sulfate solution.
[0082] Step 4: pass the magnesium sulfate solution through a precision filter of no less than 300 mesh filter media to achieve fine filtration of the magnesium sulfate solution.
[0083] Step 5: Set the temperature at 30°C and the density at 1.2t / m 3 The magnesium sulfate solution is sent to the three-effect evaporator for evaporation to obt...
PUM
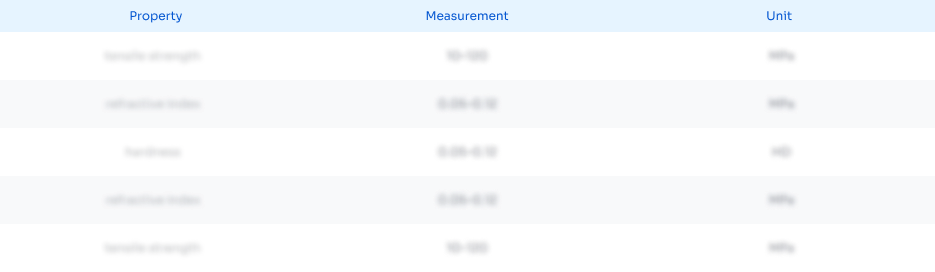
Abstract
Description
Claims
Application Information

- Generate Ideas
- Intellectual Property
- Life Sciences
- Materials
- Tech Scout
- Unparalleled Data Quality
- Higher Quality Content
- 60% Fewer Hallucinations
Browse by: Latest US Patents, China's latest patents, Technical Efficacy Thesaurus, Application Domain, Technology Topic, Popular Technical Reports.
© 2025 PatSnap. All rights reserved.Legal|Privacy policy|Modern Slavery Act Transparency Statement|Sitemap|About US| Contact US: help@patsnap.com