Polyamide, and preparation method and application thereof
A polyamide and diamine technology, applied in the polymer field, can solve problems such as unfavorable polyamide processing and gelation, and achieve the effects of low triamine content, low polyamide gel content and high service temperature
- Summary
- Abstract
- Description
- Claims
- Application Information
AI Technical Summary
Problems solved by technology
Method used
Image
Examples
preparation example Construction
[0024] A kind of preparation method of polyamide, comprises the following steps:
[0025] Feeding: Add dibasic acid monomer, diamine monomer, deionized water, optional nylon salt and other reaction aids into the reaction kettle, wherein the oxygen content of the deionized water is less than 0.05-0.1mg / L;
[0026] fill with protective gas;
[0027] Prepolymerization: Heating the reactor to make the mixture in the reactor undergo prepolymerization.
[0028] Among them, 35-50 mole parts of dibasic acid monomers, 35-50 mole parts of diamine monomers, wherein, the preferred range of the optional nylon salt is 0-30 mole parts, and the deionized water is The total amount of the reactant and water is 10-40wt%, preferably 20-30wt%.
[0029] The dibasic acid monomers include terephthalic acid and optionally oxalic acid, malonic acid, succinic acid, glutaric acid, adipic acid, pimelic acid, suberic acid, 2-methylsuberic acid, acid, azelaic acid, sebacic acid, undecanedioic acid, dod...
Embodiment 1
[0047] In the autoclave equipped with magnetic coupling stirring, condenser, gas phase port, feeding port, and pressure explosion-proof port, add the reaction raw materials according to the ratio in the table, and add deionized water. The oxygen content of the deionized water has been tested and its content is 0.01 mg / L, evacuated and filled with high-purity nitrogen as a protective gas, heated to 220°C within 2 hours under stirring, stirred the reaction mixture at 220°C for 1 hour, and then raised the temperature of the reactant to 230°C under stirring ℃. The reaction was continued at a constant temperature of 230°C and a constant pressure of 2.2MPa for 2 hours, and the pressure was kept constant by removing the formed water. After the reaction was completed, the material was discharged, and the prepolymer was vacuum-dried at 80°C for 24 hours to obtain the prepolymer. Polymerization product, the prepolymerization product is subjected to solid-phase viscosity increasing at 25...
Embodiment 2
[0049] In the autoclave equipped with magnetic coupling stirring, condenser, gas phase port, feeding port, and pressure explosion-proof port, add the reaction raw materials according to the ratio in the table, and add deionized water. The oxygen content of the deionized water has been tested and its content is 0.02 mg / L, evacuated and filled with high-purity nitrogen as a protective gas, heated to 220°C within 2 hours under stirring, stirred the reaction mixture at 220°C for 1 hour, and then raised the temperature of the reactant to 230°C under stirring ℃. The reaction was continued at a constant temperature of 230°C and a constant pressure of 2.2MPa for 2 hours, and the pressure was kept constant by removing the formed water. After the reaction was completed, the material was discharged, and the prepolymer was vacuum-dried at 80°C for 24 hours to obtain the prepolymer. Polymerization product, the prepolymerization product is subjected to solid-phase viscosity increasing at 25...
PUM
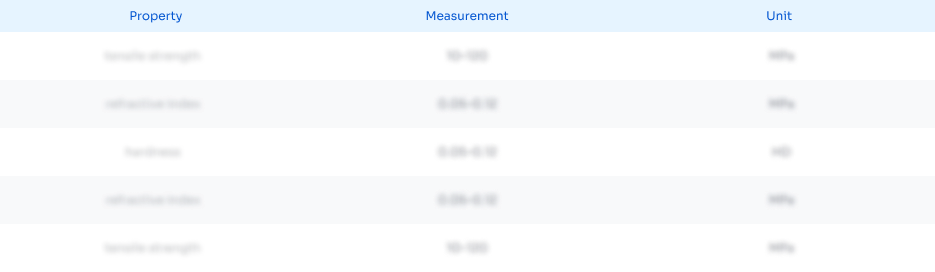
Abstract
Description
Claims
Application Information

- R&D
- Intellectual Property
- Life Sciences
- Materials
- Tech Scout
- Unparalleled Data Quality
- Higher Quality Content
- 60% Fewer Hallucinations
Browse by: Latest US Patents, China's latest patents, Technical Efficacy Thesaurus, Application Domain, Technology Topic, Popular Technical Reports.
© 2025 PatSnap. All rights reserved.Legal|Privacy policy|Modern Slavery Act Transparency Statement|Sitemap|About US| Contact US: help@patsnap.com